Witam, po upływie 11 miesięcy obudowy są sklejone.
Temat na początkowym etapie omawiany już na forum:
http://diyaudio.pl/showthread.php/26...-2-dro%C5%BCne
Dla przypomnienia monitorki 2 way na:
T.10.250.8.PCX
W.15.160.8.FCX
Założeniem jest wykonania Polskich kolumn o zadowalającej estetyce i przyzwoitym brzmieniu
Materiał obudowy drewno dębowe, front pokryty naturalną skórą.
Dotychczasowe wydatki:
Kołki pozycjonujące drewniane bukowe 9zł
deski dębowe 450zł
obróbka CNC 200zł
pasy ścierne 30zł
głośniki i tunele BR 674zł
śruby mocujące głośniki 3,5zł
wkładki gwintowe 44,5zł
politura szelakowa 30zł
rozwiertak nastawny Fi10 43zł
klej do drewna 17zł
klej do skóry 38,5zł
skóra 38,5zł
papier ścierny 5,4zł
elementy zwrotnicy 177,5zł
jig 75,5zł
przyrząd do frezowania krawędzi 43zł
łożysko do freza 20zł
suma na ten moment 1900zł
Zostaje jeszcze do zakupu:
terminale przyłączeniowe,
kable
wtyczki
materiał maskownicy
magnesy do maskownicy
wydruk 3D ramki maskownic
Przedstawiam kilka fotek z budowy:
Koncept
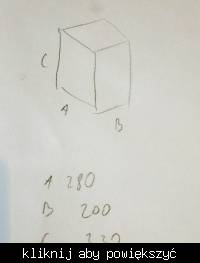
Prace projektowe

Model monitorka
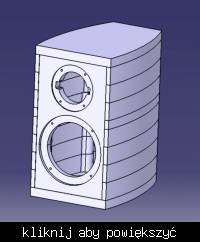
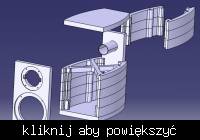
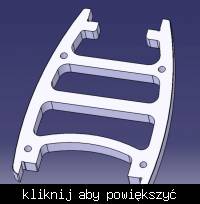
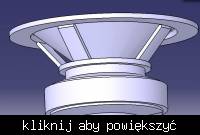
Symulacja po zmianie koncepcji żebra wzmacniającego
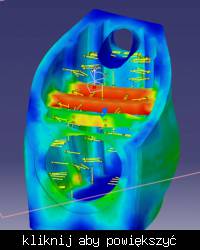
Materiał na obudowy
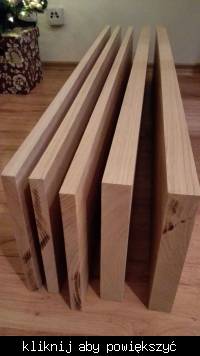
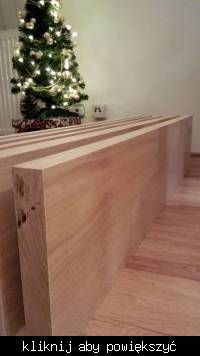
Elementy po obróbce
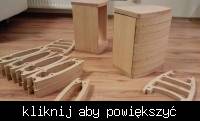
Głośniki
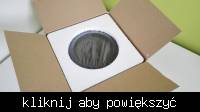
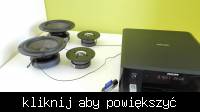
Pierwsze szlify
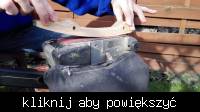
Śruby i wkładki gwintowe
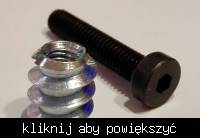
Elementy ułożone jak jenga (próba wyobrażenia sobie jak to będzie wyglądało)
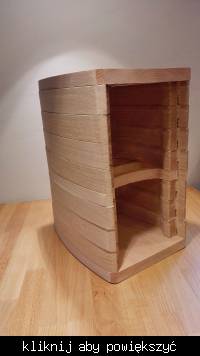
Jako że podczas obróbki wystąpiły nieoczekiwane przeszkody, trzeba było poprawić otwory i nadać im właściwy wymiar (użyłem rozwiertaka nastawnego Fi10)
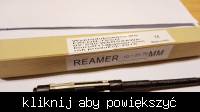
Ale najpierw i potem zresztą też, trzeba było wykonać fazki na krawędziach otworów (użyłem kulistego kamienia szlifierskiego i multiszlifierki)
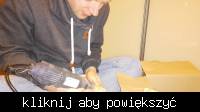
Rozwiercanie otworów było mozolne (dla zwiększenia wydajności użyłem wkrętarki do napędu zamiast ręcznego pokrętła)
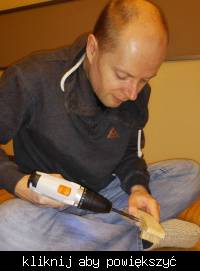
Pierwsza warstwa szelaku dla zabezpieczenia elementów przed zabrudzeniem klejem itp.
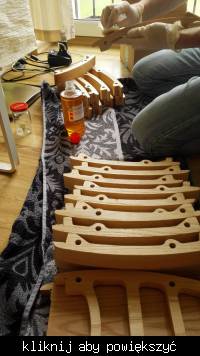
Parowanie elementów pod kątem struktury drewna dla lepszego efektu wizualnego i znakowanie elementów
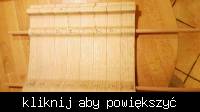
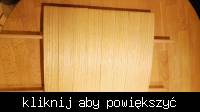
Jig
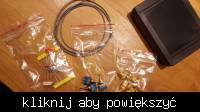
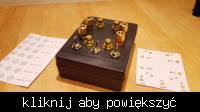
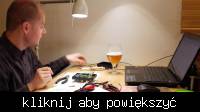
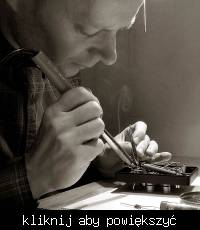

Skrzynka szczelna dla wykonania pomiaru TS obydwiema metodami, oraz pomiary rezonansu oscyloskopem (wyszło ponad 10Hz więcej niż w danych producenta)
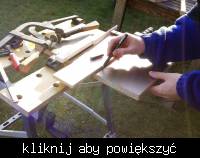
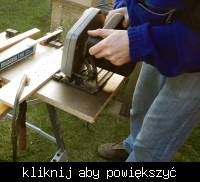
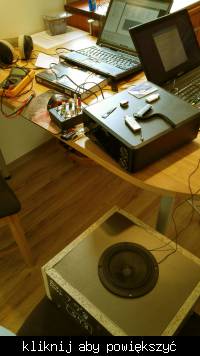
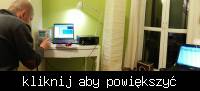
Elementy zwrotnicy
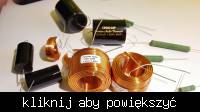
Przyrząd do frezowania gniazd pod głośniki i efekt frezowania
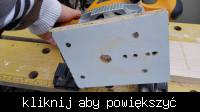
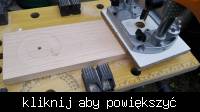
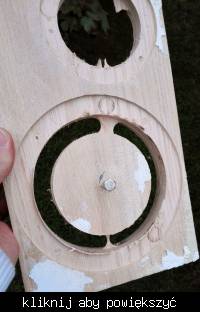
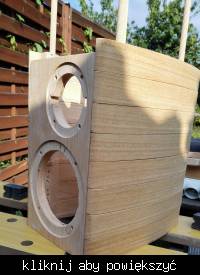

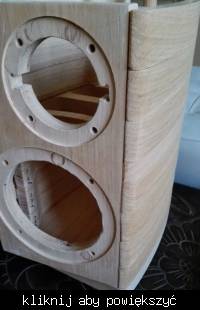

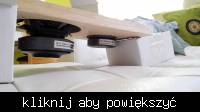
Przyrząd do frezowania krawędzi frontu i tyłu (wyrównywanie boków i dna gniazda)
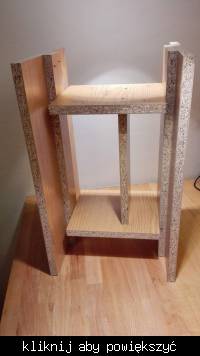
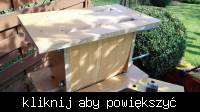
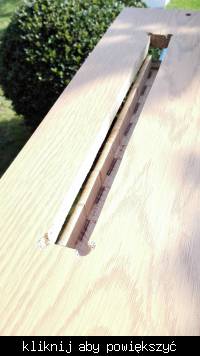
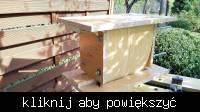
Dopasowywanie frontów i tyłów to rzeczywistej wysokości boków i krzywizn denka i wieka
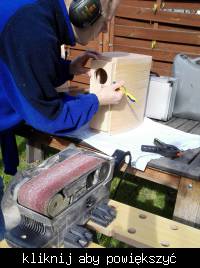
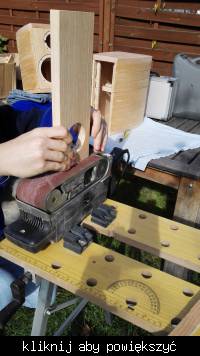
Frezowanie zaokrągleń na obudowie
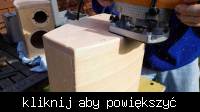
Przyszła skóra naturlna na fronty
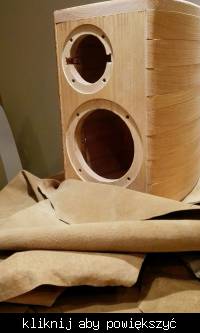
Przeróbka freza wyrównującego na frez który na określonej głębokości skrawa określoną warstwę materiału i prowadzi się po rzeczywistej powierzchni (krzywej)(jak zaznaczyłem wcześniej całość dopasowałem do krzywizn jakie powstały po wielu miesiącach) łożysko na zamówienie ¼” x3/8”x 1/8” Frezowałem tym krawędź na której będzie wklejona skóra (resztę zostawiłem oby połączenie klejowe z resztą obudowy było solidne i szczelne.
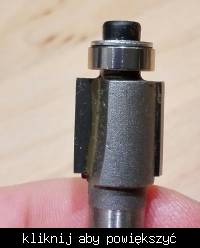
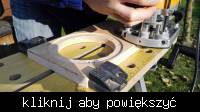
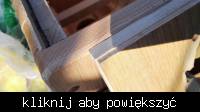
Wkręcanie wkładek gwintowych pod śruby z gwintem metrycznym
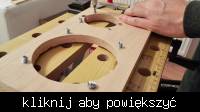
Klejenie wikolowym klejem klasy D3 na prasie hydraulicznej z użyciem pasów transportowych (zastosowałem nacisk 2,5 tony aby złącza klejowe były najcieńsze)
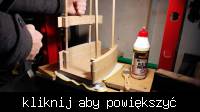
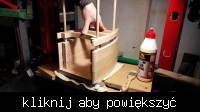
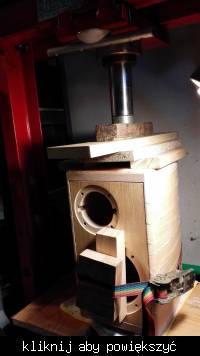
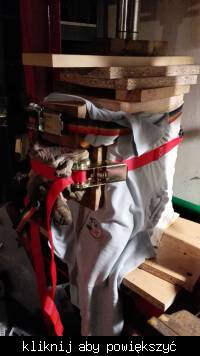
Efekt po klejeniu jest zadowalający
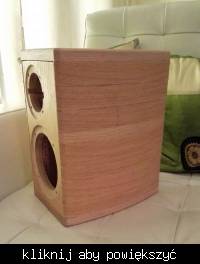
Na wszelki wypadek postanowiłem uszczelnić połączenia klejem za pomocą strzykawki z igła
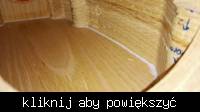
Jak widać proces budowy się przedłuża z uwagi na problemogenny charakter konstrukcji. Następnym krokiem jest szlifowanie wykańczające obudowy i nasączenie szelakiem, klejenie skóry, woskowanie ...
Temat na początkowym etapie omawiany już na forum:
http://diyaudio.pl/showthread.php/26...-2-dro%C5%BCne
Dla przypomnienia monitorki 2 way na:
T.10.250.8.PCX
W.15.160.8.FCX
Założeniem jest wykonania Polskich kolumn o zadowalającej estetyce i przyzwoitym brzmieniu
Materiał obudowy drewno dębowe, front pokryty naturalną skórą.
Dotychczasowe wydatki:
Kołki pozycjonujące drewniane bukowe 9zł
deski dębowe 450zł
obróbka CNC 200zł
pasy ścierne 30zł
głośniki i tunele BR 674zł
śruby mocujące głośniki 3,5zł
wkładki gwintowe 44,5zł
politura szelakowa 30zł
rozwiertak nastawny Fi10 43zł
klej do drewna 17zł
klej do skóry 38,5zł
skóra 38,5zł
papier ścierny 5,4zł
elementy zwrotnicy 177,5zł
jig 75,5zł
przyrząd do frezowania krawędzi 43zł
łożysko do freza 20zł
suma na ten moment 1900zł
Zostaje jeszcze do zakupu:
terminale przyłączeniowe,
kable
wtyczki
materiał maskownicy
magnesy do maskownicy
wydruk 3D ramki maskownic
Przedstawiam kilka fotek z budowy:
Koncept
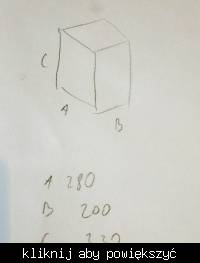
Prace projektowe

Model monitorka
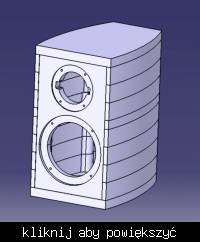
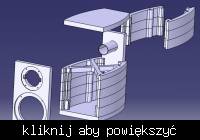
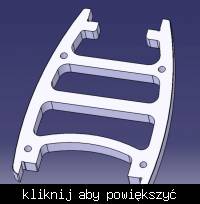
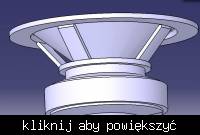
Symulacja po zmianie koncepcji żebra wzmacniającego
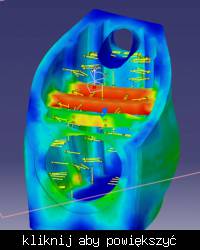
Materiał na obudowy
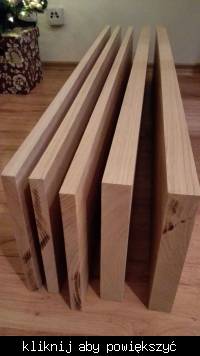
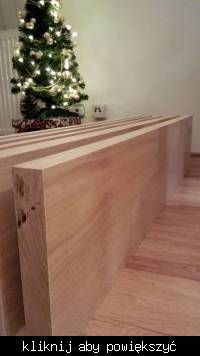
Elementy po obróbce
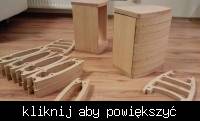
Głośniki
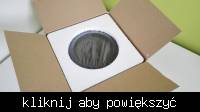
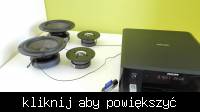
Pierwsze szlify
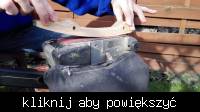
Śruby i wkładki gwintowe
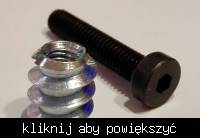
Elementy ułożone jak jenga (próba wyobrażenia sobie jak to będzie wyglądało)
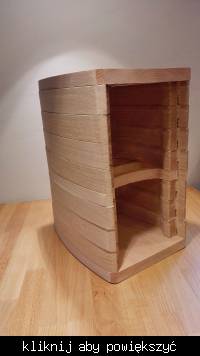
Jako że podczas obróbki wystąpiły nieoczekiwane przeszkody, trzeba było poprawić otwory i nadać im właściwy wymiar (użyłem rozwiertaka nastawnego Fi10)
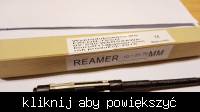
Ale najpierw i potem zresztą też, trzeba było wykonać fazki na krawędziach otworów (użyłem kulistego kamienia szlifierskiego i multiszlifierki)
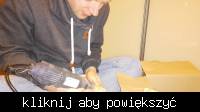
Rozwiercanie otworów było mozolne (dla zwiększenia wydajności użyłem wkrętarki do napędu zamiast ręcznego pokrętła)
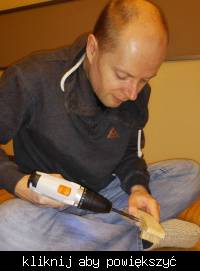
Pierwsza warstwa szelaku dla zabezpieczenia elementów przed zabrudzeniem klejem itp.
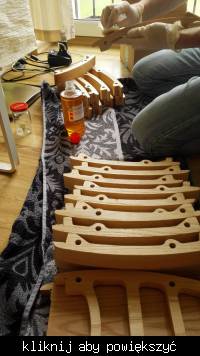
Parowanie elementów pod kątem struktury drewna dla lepszego efektu wizualnego i znakowanie elementów
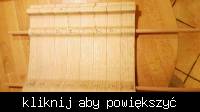
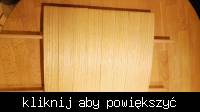
Jig
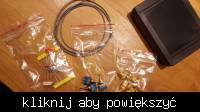
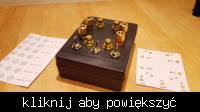
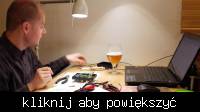
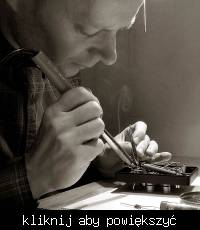

Skrzynka szczelna dla wykonania pomiaru TS obydwiema metodami, oraz pomiary rezonansu oscyloskopem (wyszło ponad 10Hz więcej niż w danych producenta)
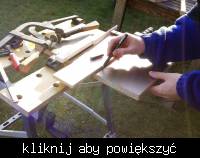
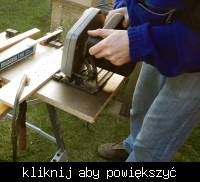
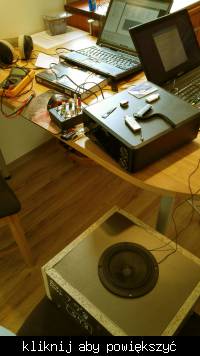
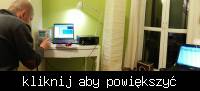
Elementy zwrotnicy
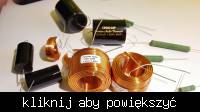
Przyrząd do frezowania gniazd pod głośniki i efekt frezowania
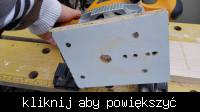
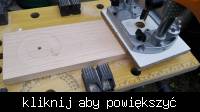
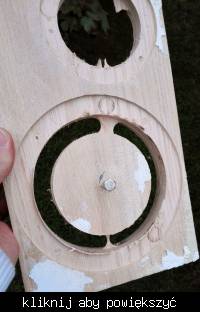
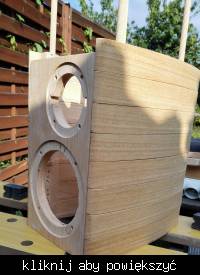

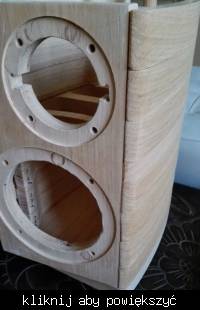

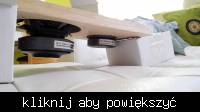
Przyrząd do frezowania krawędzi frontu i tyłu (wyrównywanie boków i dna gniazda)
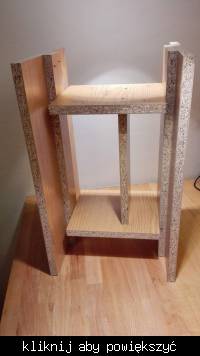
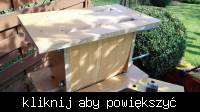
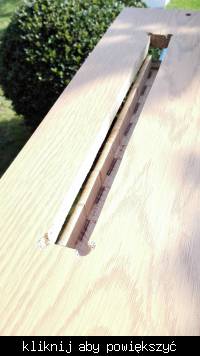
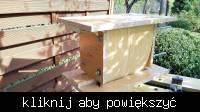
Dopasowywanie frontów i tyłów to rzeczywistej wysokości boków i krzywizn denka i wieka
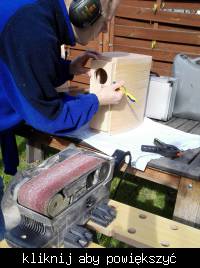
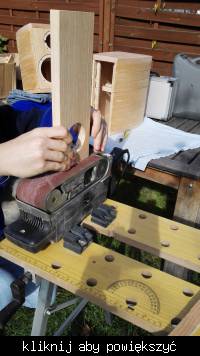
Frezowanie zaokrągleń na obudowie
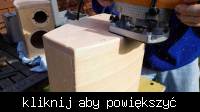
Przyszła skóra naturlna na fronty
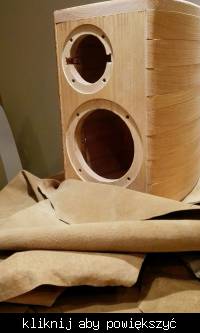
Przeróbka freza wyrównującego na frez który na określonej głębokości skrawa określoną warstwę materiału i prowadzi się po rzeczywistej powierzchni (krzywej)(jak zaznaczyłem wcześniej całość dopasowałem do krzywizn jakie powstały po wielu miesiącach) łożysko na zamówienie ¼” x3/8”x 1/8” Frezowałem tym krawędź na której będzie wklejona skóra (resztę zostawiłem oby połączenie klejowe z resztą obudowy było solidne i szczelne.
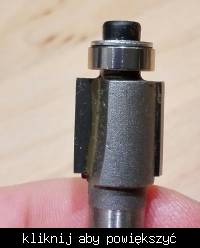
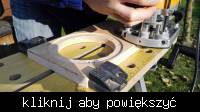
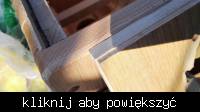
Wkręcanie wkładek gwintowych pod śruby z gwintem metrycznym
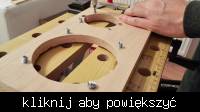
Klejenie wikolowym klejem klasy D3 na prasie hydraulicznej z użyciem pasów transportowych (zastosowałem nacisk 2,5 tony aby złącza klejowe były najcieńsze)
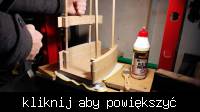
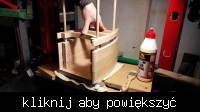
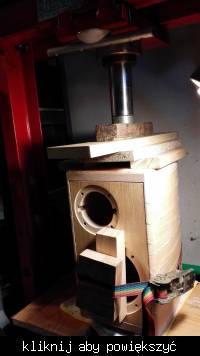
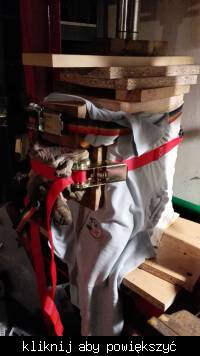
Efekt po klejeniu jest zadowalający
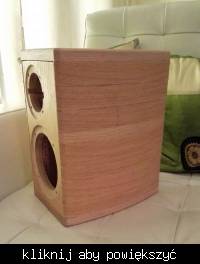
Na wszelki wypadek postanowiłem uszczelnić połączenia klejem za pomocą strzykawki z igła
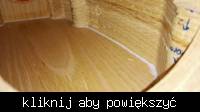
Jak widać proces budowy się przedłuża z uwagi na problemogenny charakter konstrukcji. Następnym krokiem jest szlifowanie wykańczające obudowy i nasączenie szelakiem, klejenie skóry, woskowanie ...
Skomentuj