Założenia projektu - budżetowe monitory na sprawdzonych przetwornikach o świetnym stosunku cena/jakość.
Projekt powstał dzięki pomocy forumowicza Branża z zap-audio.pl , który mimo nawału pracy zgodził się zrobić profesjonalne pomiary i zaprojektować filtrację oraz udzielił niezbędnych wskazówek dotyczących samej obudowy.
Dziękuje również Pawłowi S. i Pogromcy Mitów za cenne rady dotyczące budowy i wykończenia.
Wszelkie dane dotyczące budowy zwrotnicy w różnych wariantach oraz rozmieszczenie wytłumienia dostępne tutaj:
http://diyaudio.pl/showthread.php/28...by-Bran%C5%BCa
Materiał - sklejka 15 mm + HDF 3 mm (poza frontem i tyłem)
Wymiary zewnętrzne (po wykończeniu fornirem):
wysokość - 45cm
szerokość - 21cm
głębokość - 26cm
litraż komory 16 litrów netto
ostatecznie zastosowałem jedno poziome wzmocnienie powyżej portu BR
*jak będę miał dostęp do drugiego komputera dodam zwymiarowany rzut aby wszystko było jasne.
Projekt frontu:
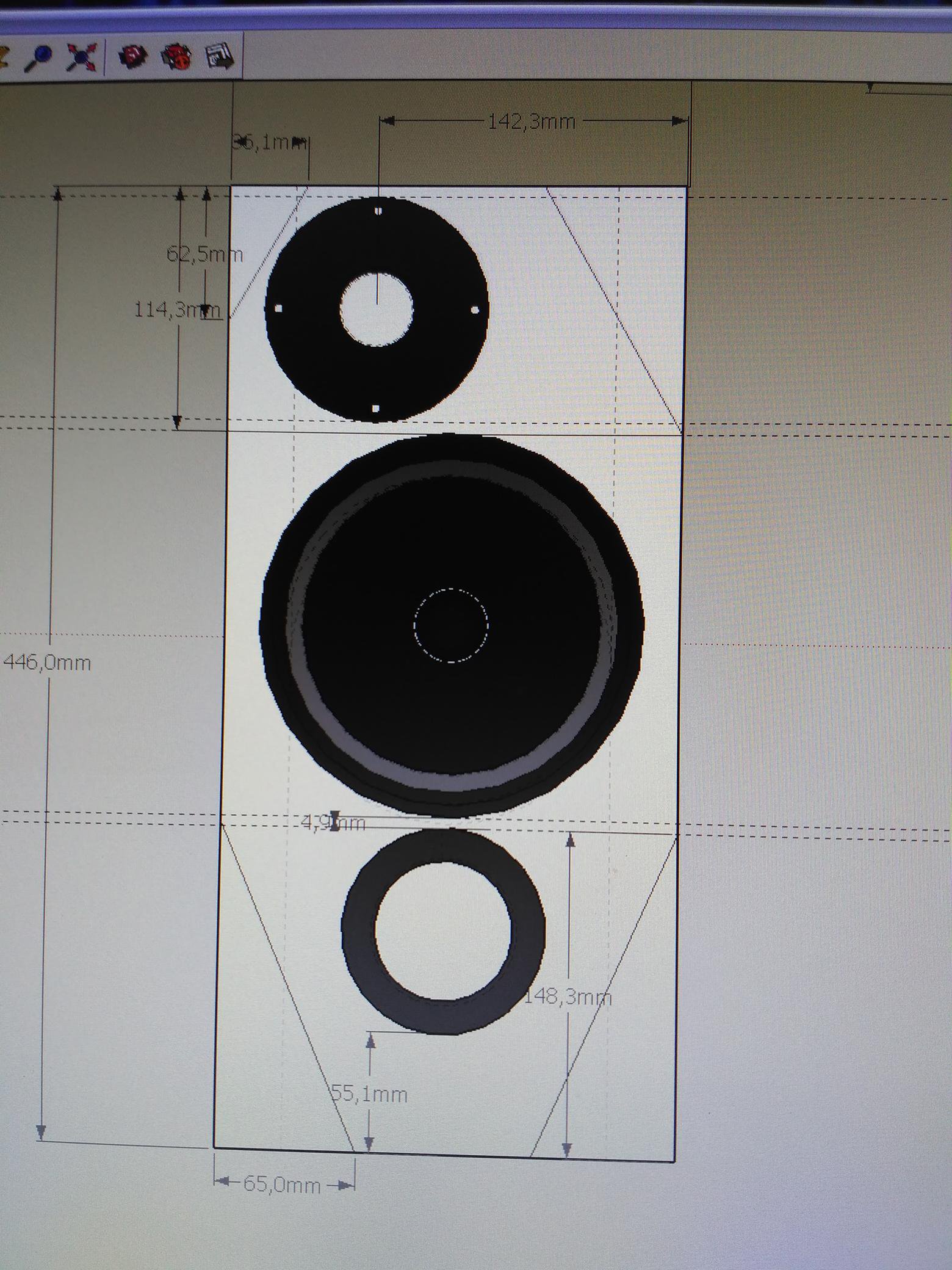
Ponieważ projekt może być ciekawą i niedrogą alternatywą dla początkujących, poniżej opisuje etap budowy właśnie z perspektywy początkującego, uwzględniając
parę pułapek, które każdy doświadczony dobrze zna.
Opis budowy:
Planowałem obudowę z MDF ale w pozostałościach trafił się kawałek sklejki 15 mm.
Zaplanowałem optymalny rozkrój i rozrysowałem go na płycie tak jak w programie czyli liniami pomiędzy którymi prowadziłem ostrze.
Odstępy ok 5 mm ze względu na cięcie zgrubne wyrzynarką średniej jakości, która potrafi ciąć pod lekkim kątem. Opłaciło się, bo margines faktycznie się przydał.
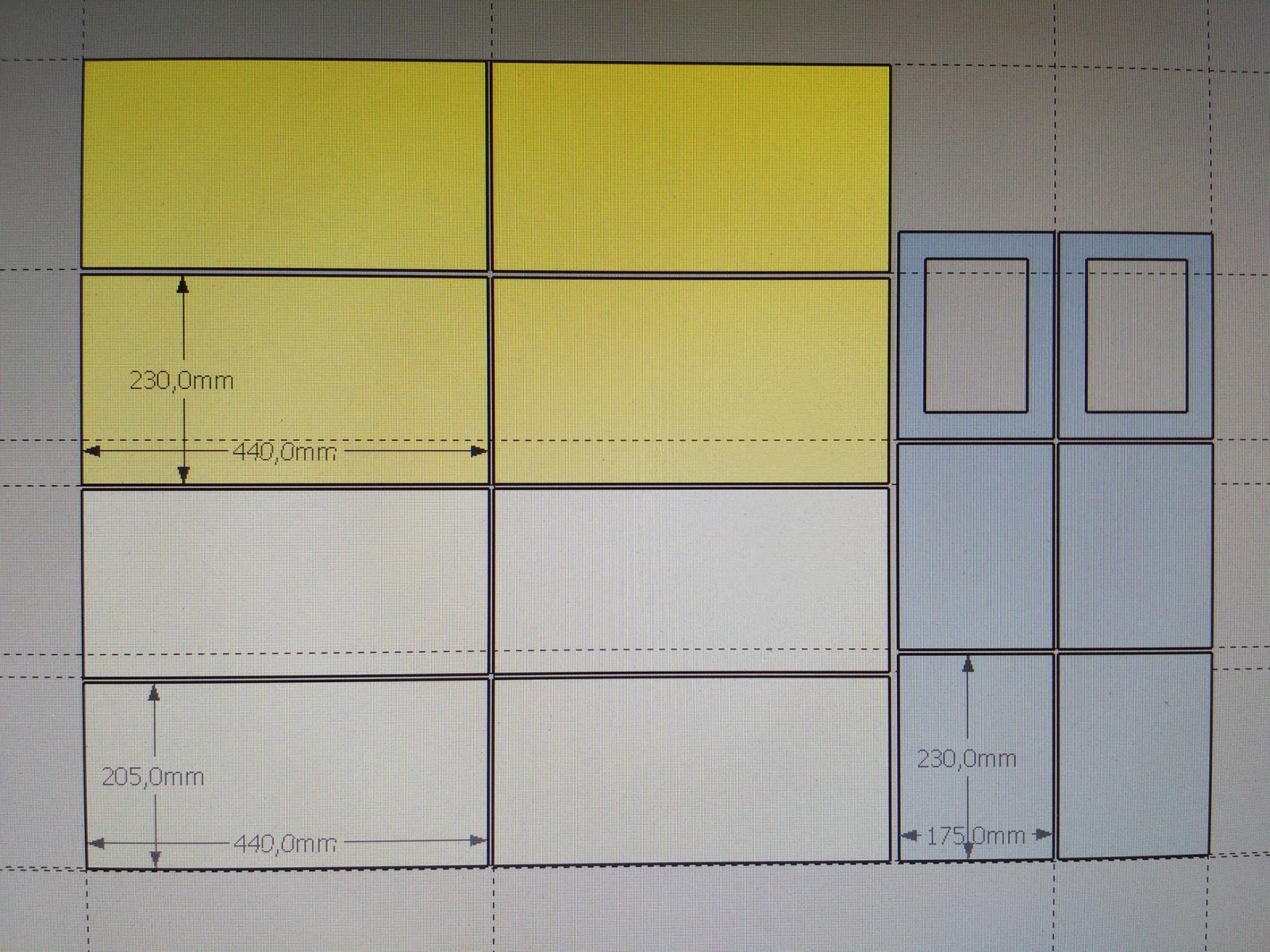
Z aluminiowego kątownika przygotowałem krawędź do frezowania pierwszych elementów.
Jak widać po rozkroju potrzebowałem przygotować jako matryce tylko 3 różne prostokąty - reszta to powielanie.
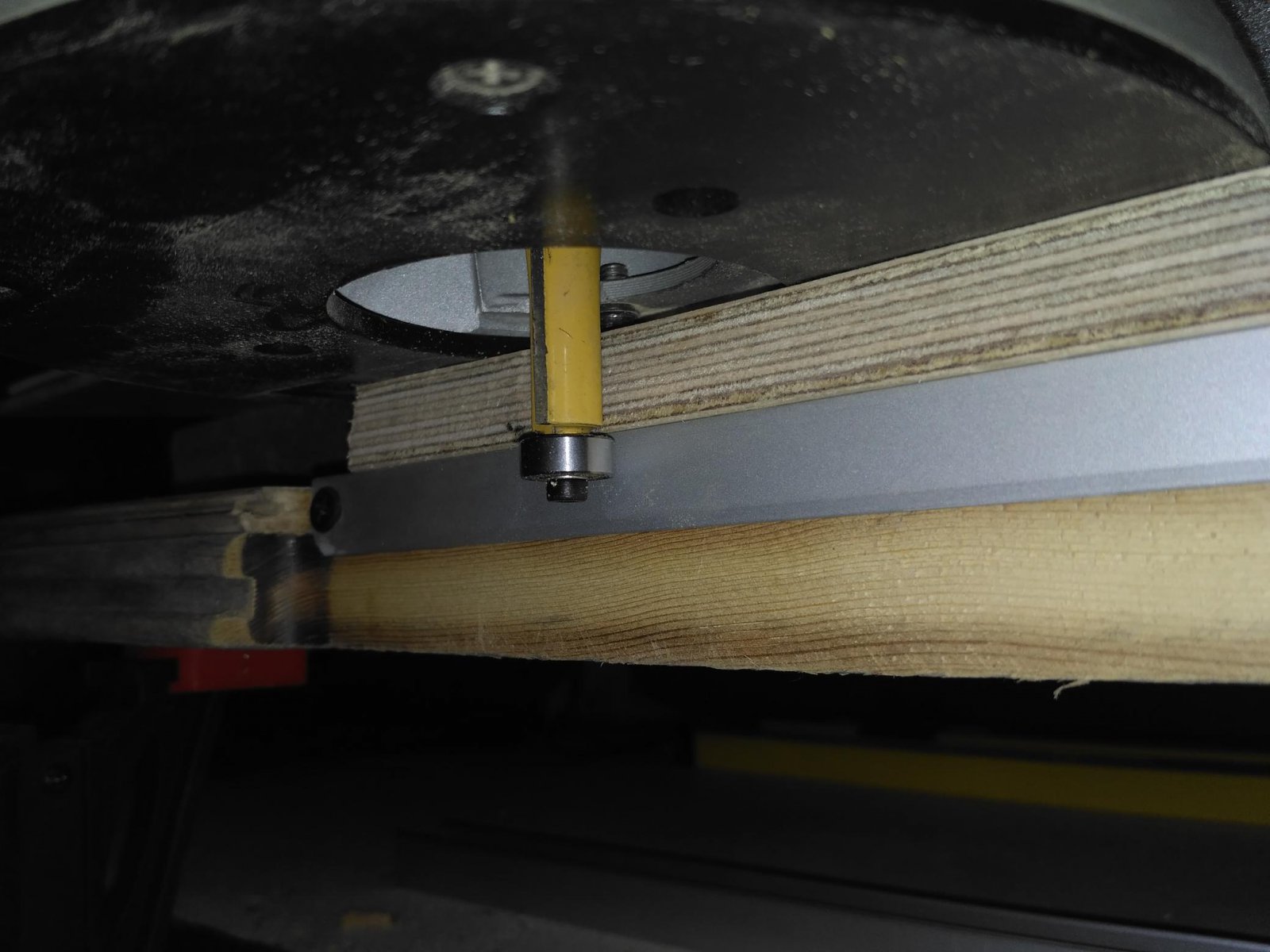
W czasie budowy pomógł mi filmik instruktażowy Pawła:
Kopiowanie kolejnych elementów frezem kopiującym- jednoręczny ścisk bardzo ułatwia pracę w pojedynkę (użyłem najtańszych z Casto za 15 zł/szt ).
Nie polecam zestawów żółtych frezów z allegro - są liche i większości pewnie nigdy nie użyjecie. Hard Head z Juli dają radę i są na sztuki.
Aby lepiej ustabilizować większe elementy przekładałem je papierem ściernym.
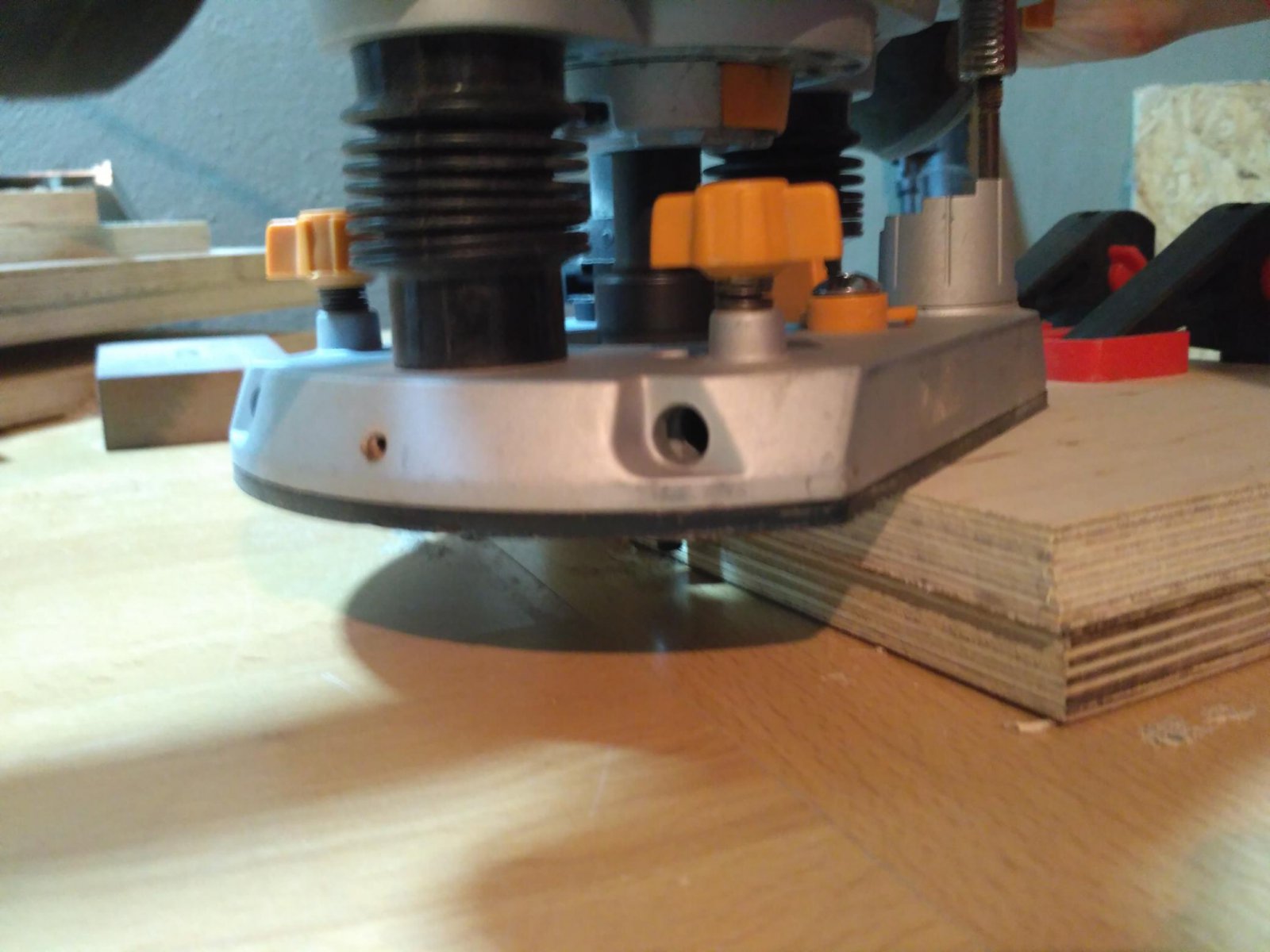
Ponieważ kupiłem gniazda z krótkim gwintem musiałem wyfrezować rowek po wewnętrznej stronie tylnych ścianek.
Wymierzyłem odległości rowka od krawędzi i zapisałem aby po ofornirowaniu wiedzieć gdzie wiercić.
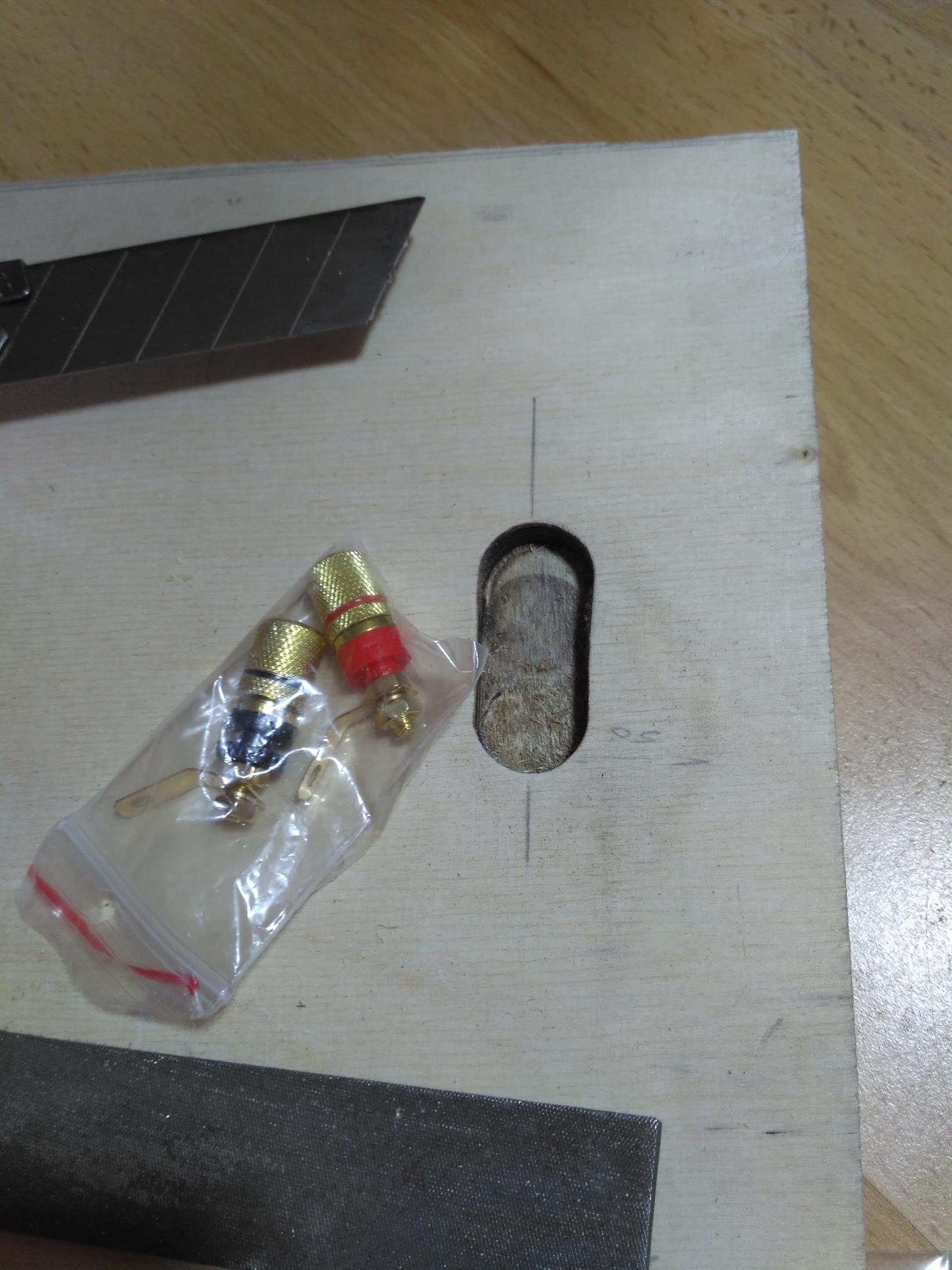
Rozpocząłem składanie. Kątowe ściski Wolfcraft bardzo się przydały. Używałem wkrętów do drewna,
które po związaniu wykręcałem. Otworki po wkrętach na tyłach i frontach (nie były oklejane HDFem) zaszpachlowałem
wiórami z klejem.
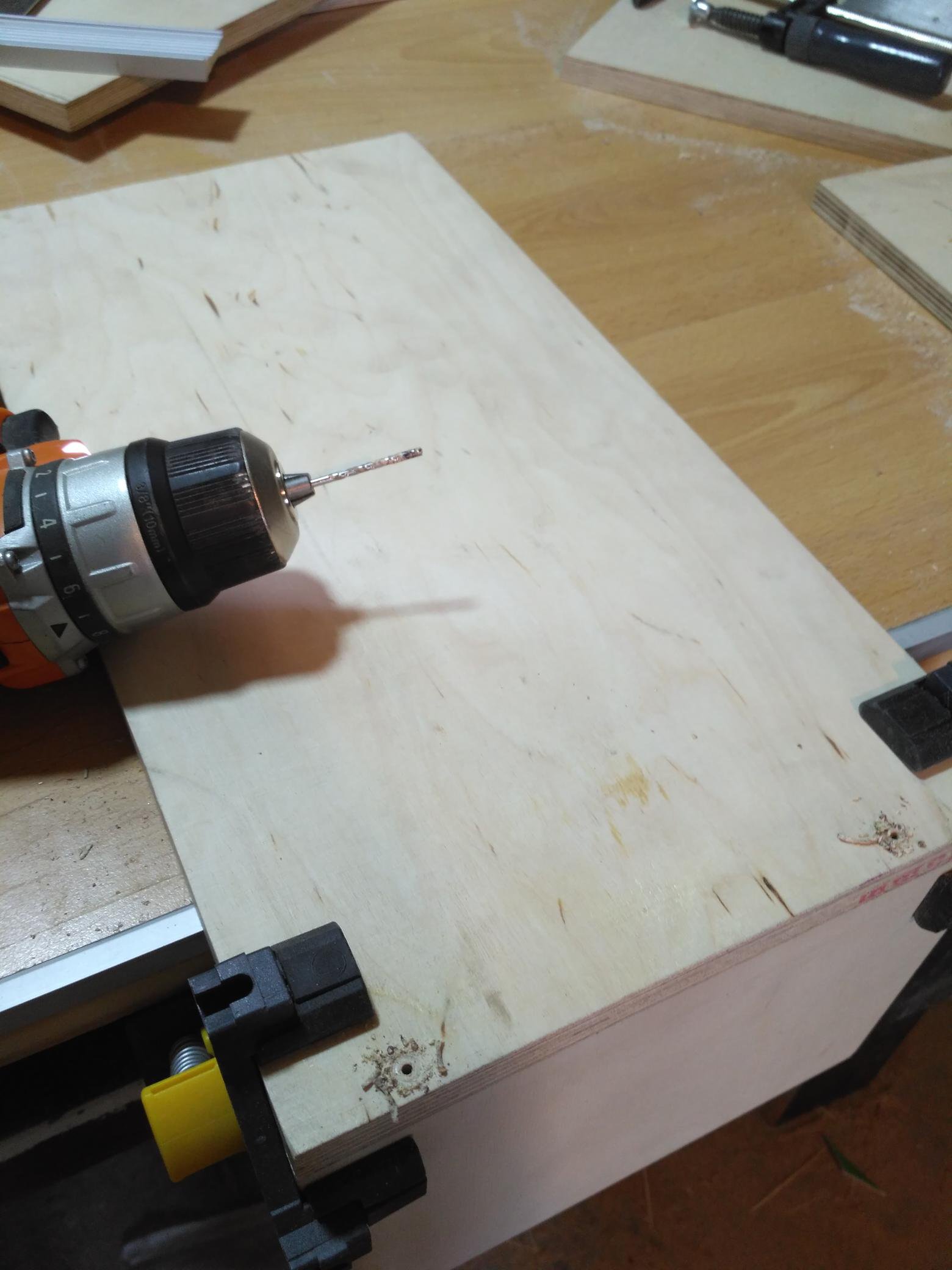
Przygotowanie wzmocnień. Ponieważ miały być możliwie w połowie wysokości kolumny, widać podcięcie na dolną część kosza głośnika średnio niskotonowego.
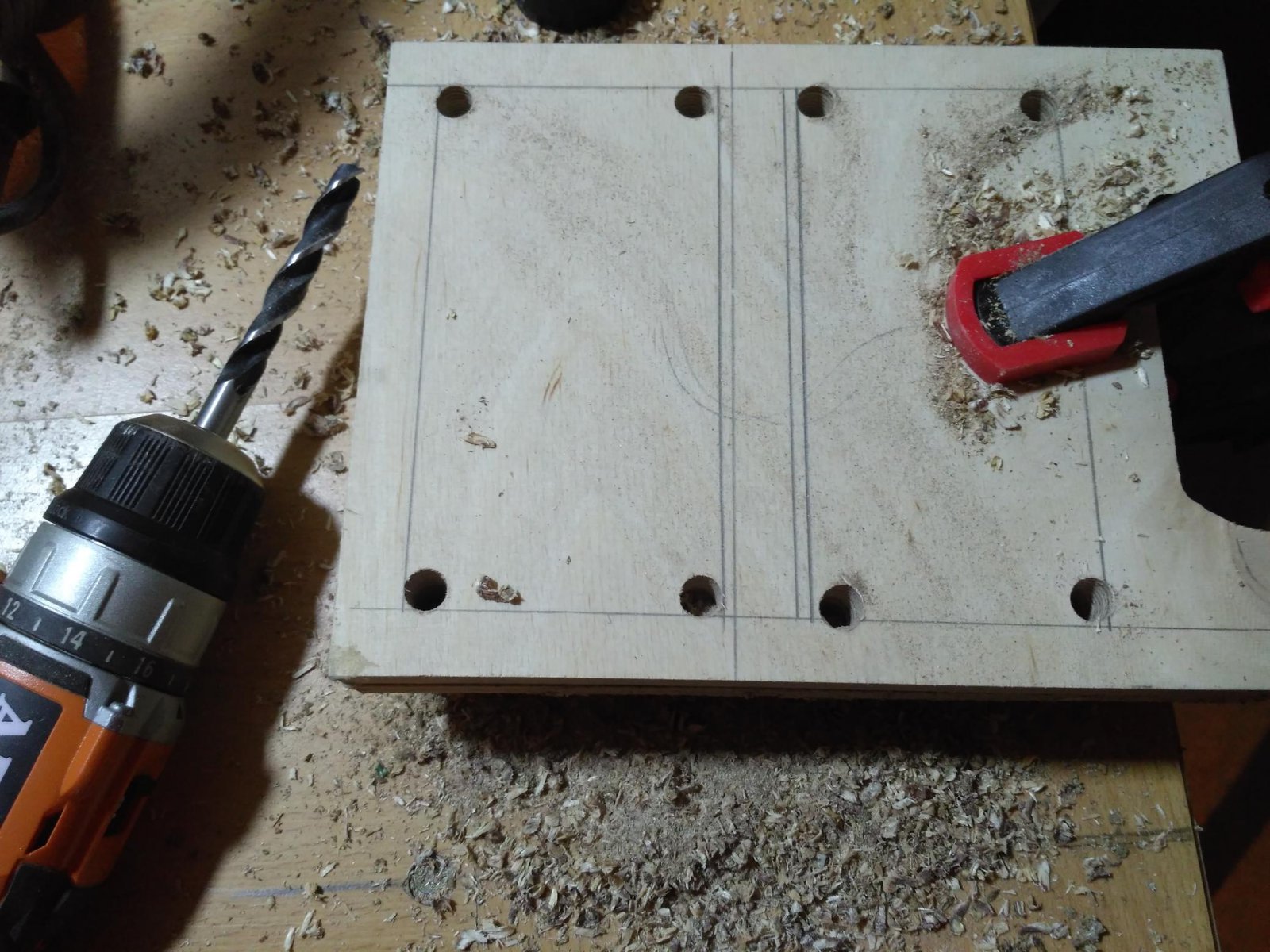
Wklejanie wzmocnień - przy okazji widać trójkąty wklejone w miejscach planowanych ścięć frontów (poza małym ścięciem przy wysokotonówce). Nie zrobiłem podwójnej ścianki frontowej
ponieważ nie chciałem zwiększać wymiarów kolumn.
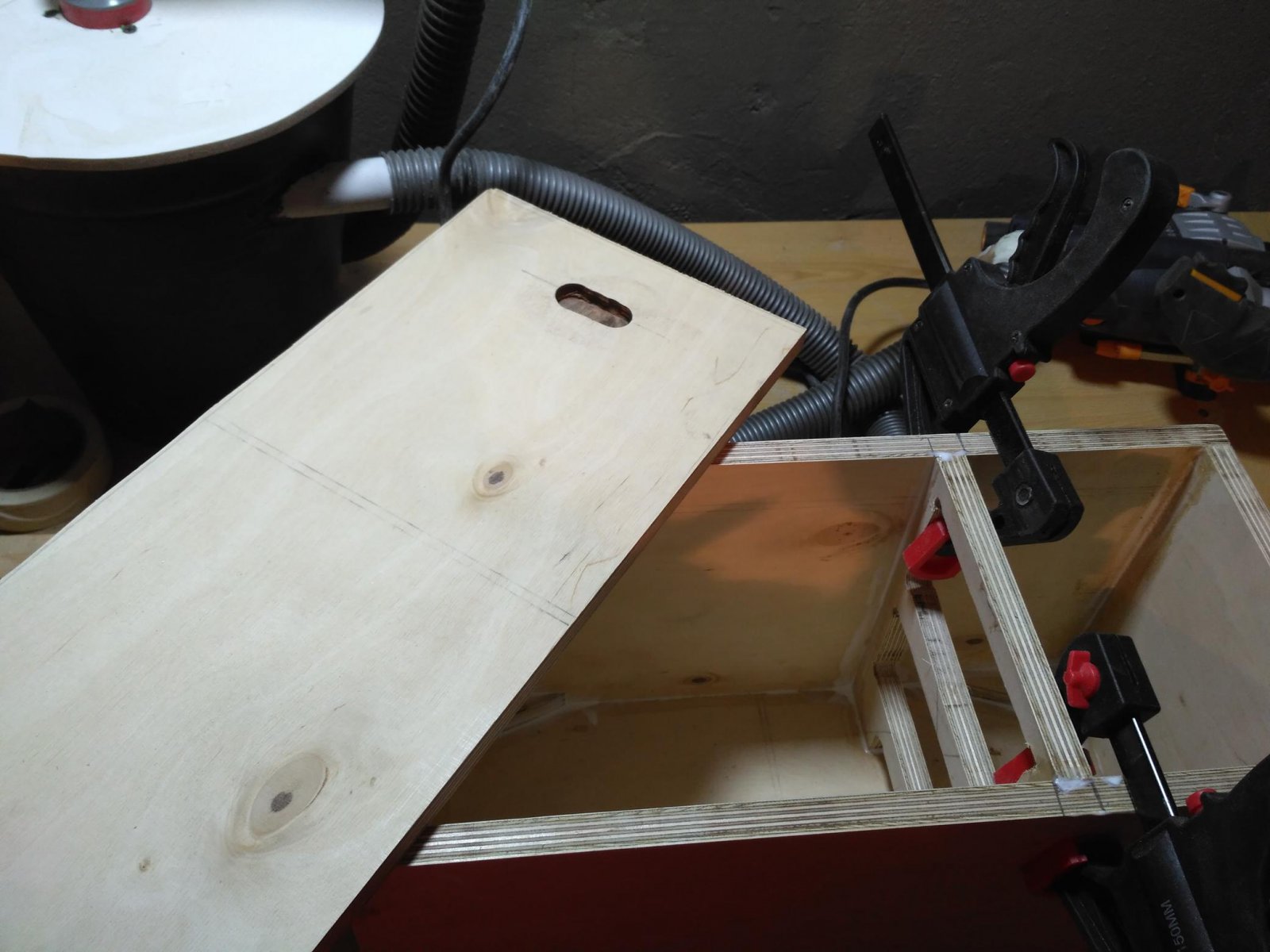
Tak się kończy frezowanie w niedzielę - na szybko, żeby jedynie umiarkowanie w*rwić neurotyczno-kompulsywną sąsiadkę z Zespołem Tourett'a...
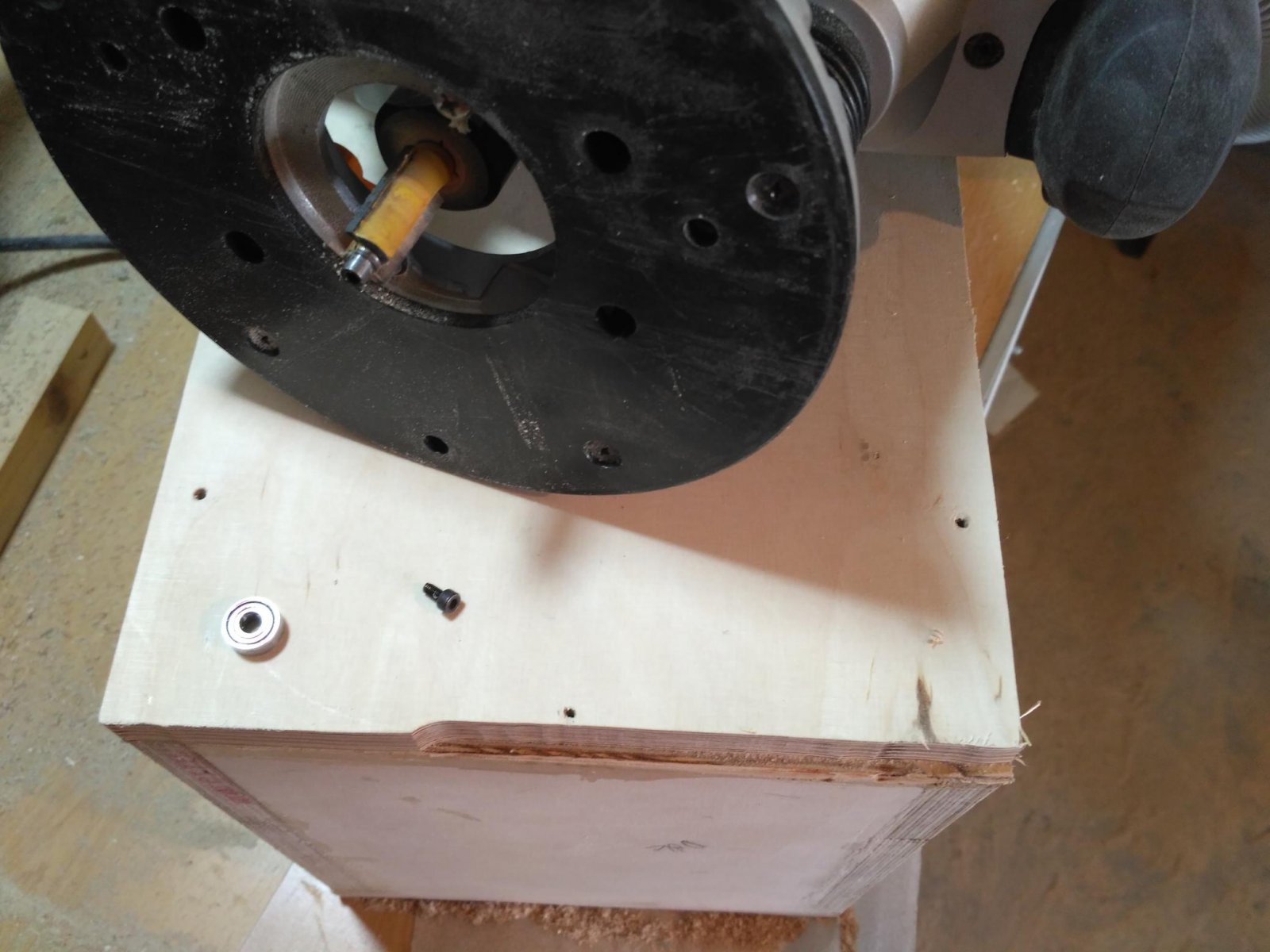
W poszukiwaniu Świętego Graala DIYowców, czyli "fosfatowanych wkrętów z niestożkowym łbem w cenie tych ze stożkowym"...
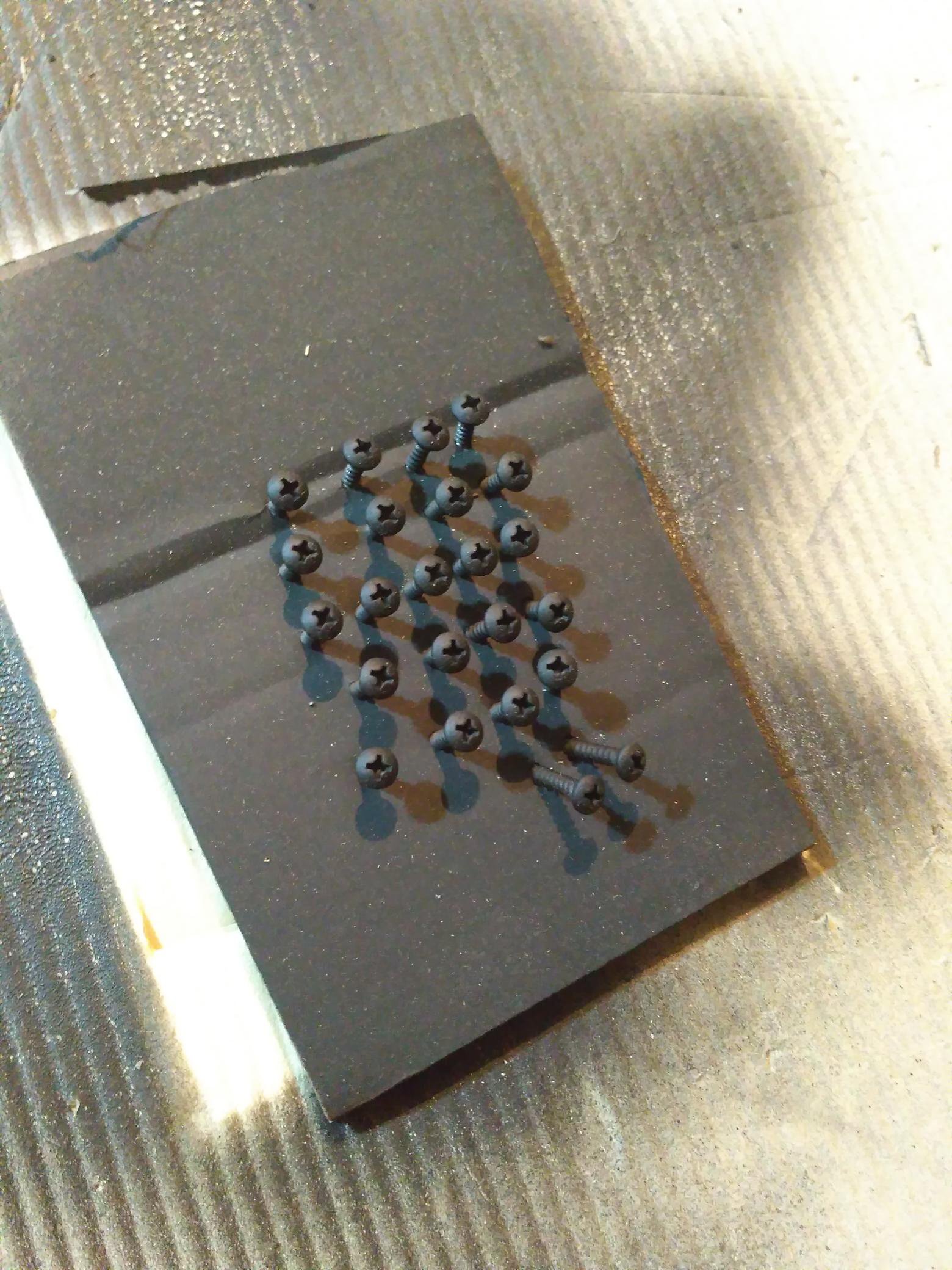
Etap oklejania płytami HDF (przeciwdziałanie klawiszowaniu). Aby płyty nie rozjeżdżały się przy docisku
stabilizowałem je listewkami przybijanymi na zszywki - sprawdziło się dobrze, ale warto pamiętać o zabezpieczeniu krawędzi kolumny przed wyciekającym klejem taśmą malarską.
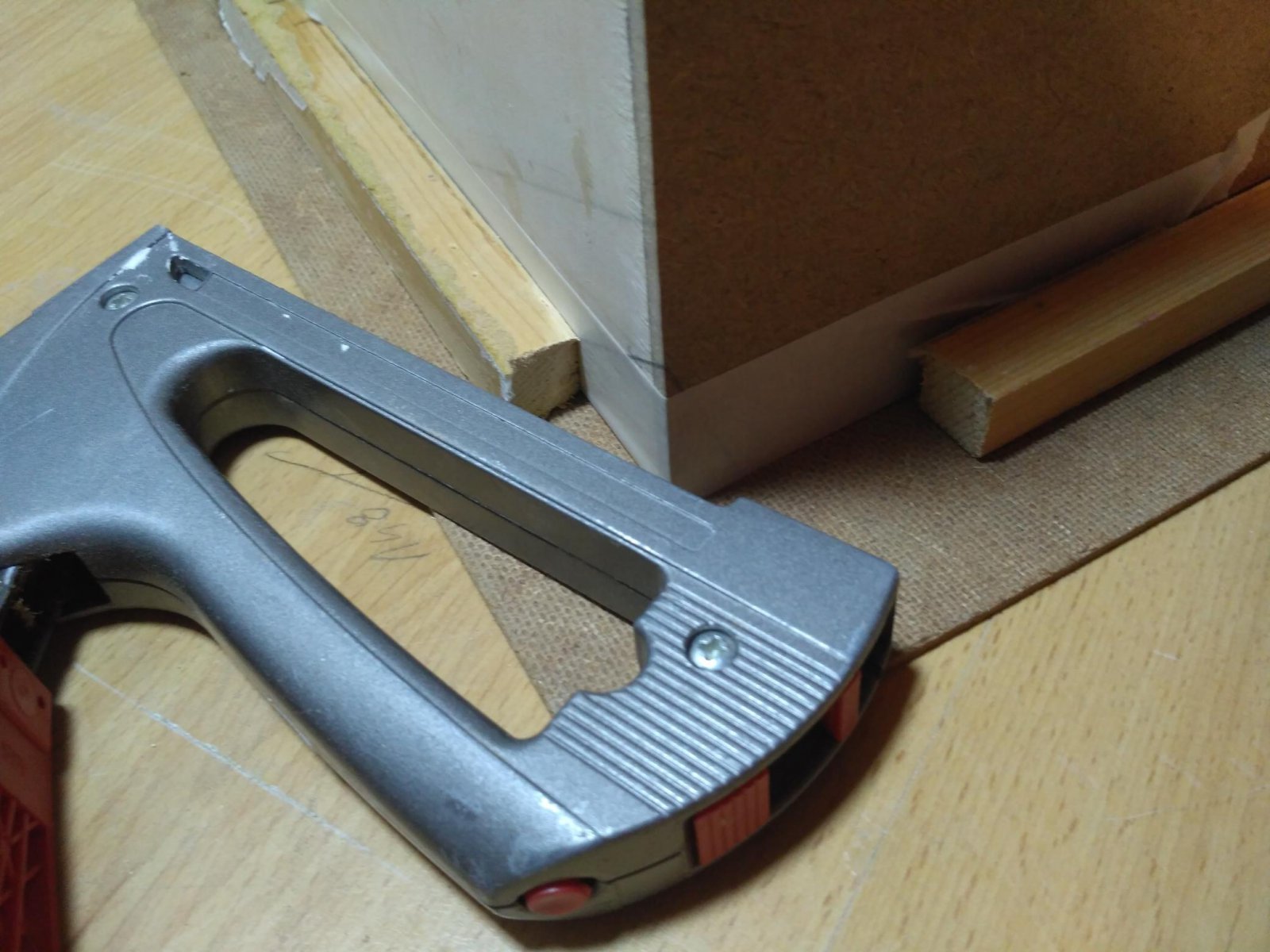
Jako przekładki użyłem piankowych płyt pod panele. Pod kołami też jest obciążenie - prasa godna Gutenberga.
Ze względu na klej zdobiący festonami ścianki z ochotą wprost proporcjonalną do generowanej siły nacisku, warto zawczasu cenzurować szmatką.
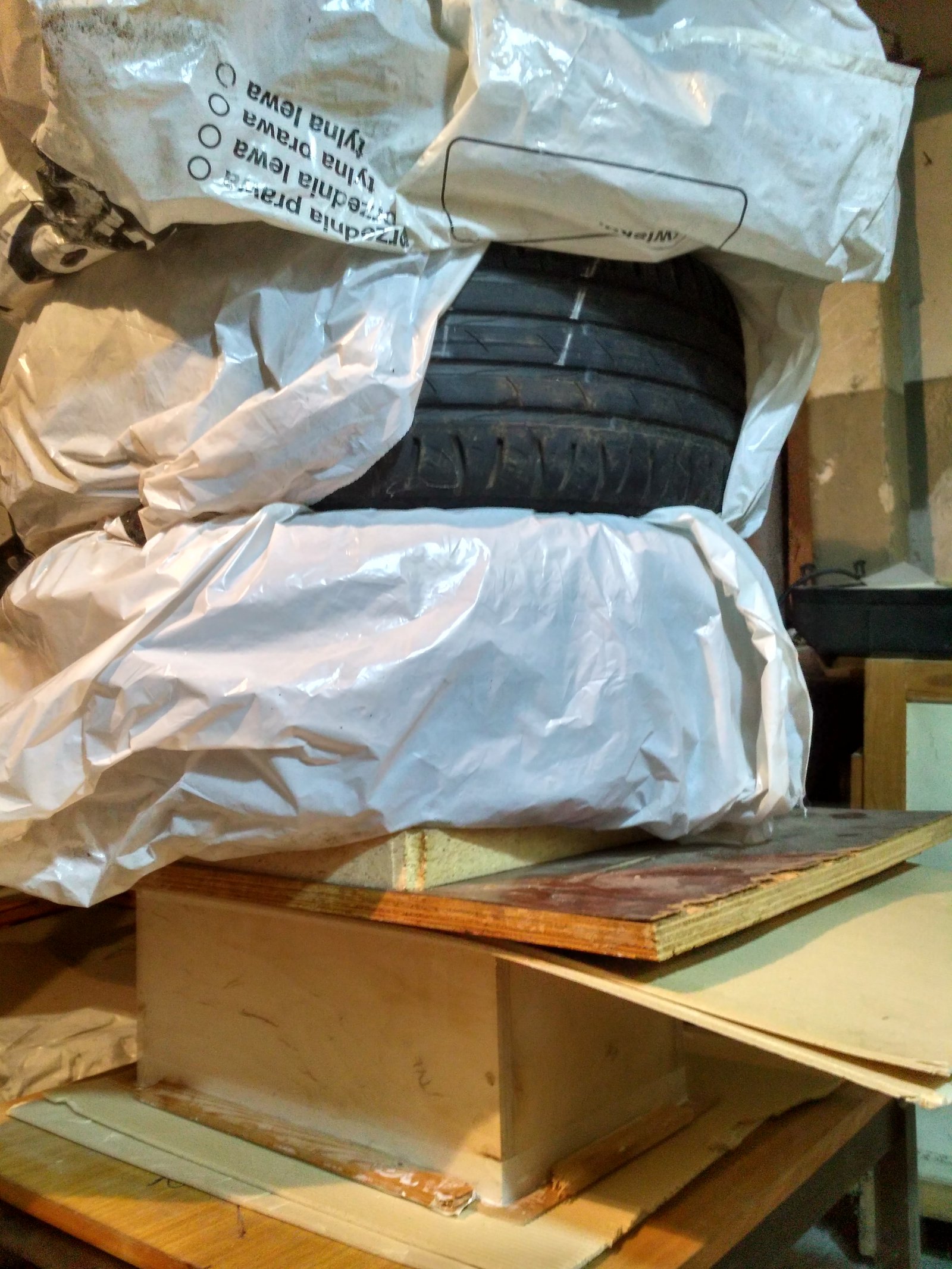
...pół-maska Irudek - polecam ze względu na tanie, nakładane na filtry pady przeciwpyłowe (ok 3zł/para) .
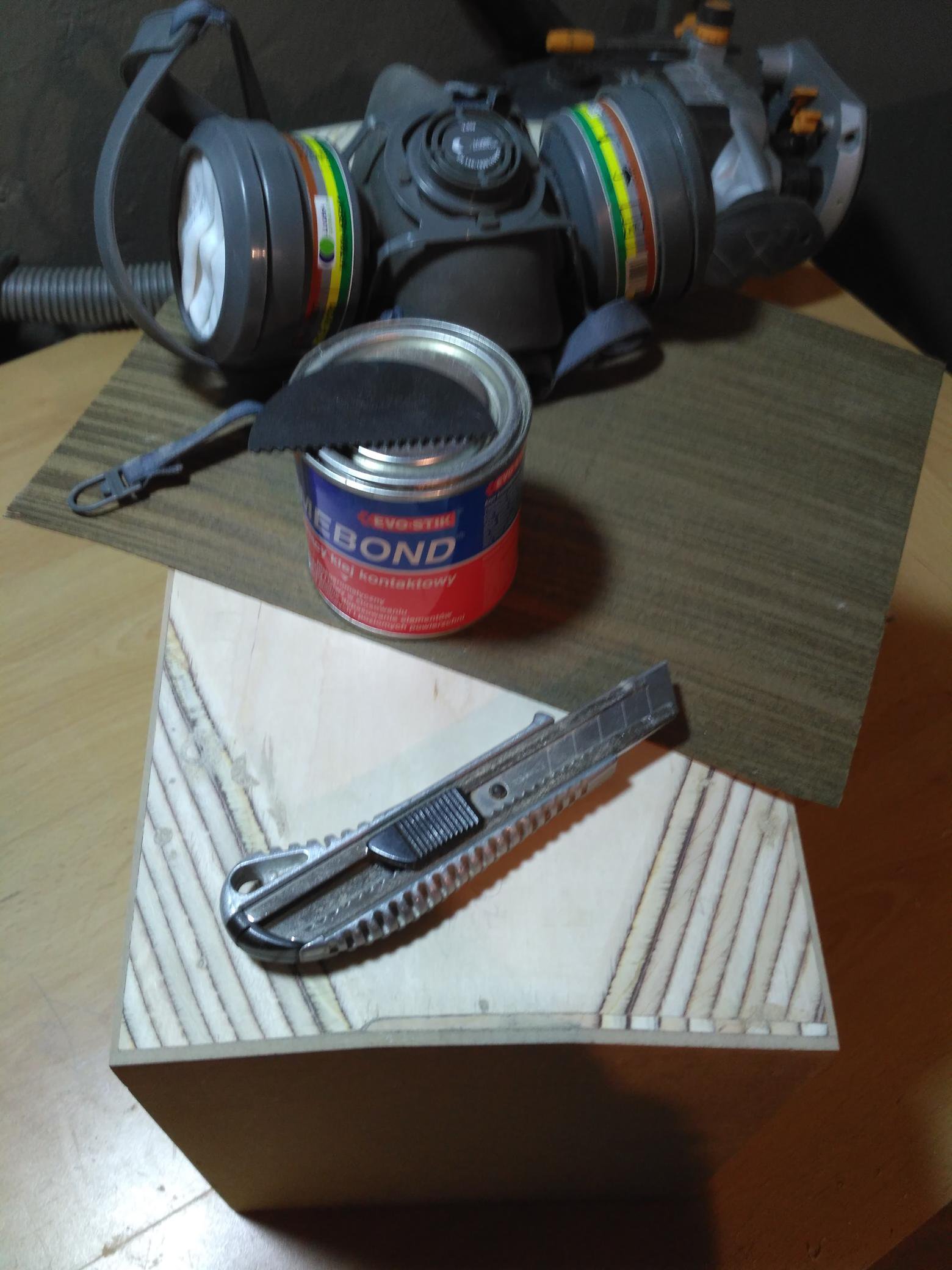
Przygotowanie forniru - warto zrobić sobie przymiar podklejony papierem ściernym, żeby nie jeździł i używać nożyka z okrągłym ostrzem.
Każdy odcinek ciąłem po kilka/kilkanaście przebiegów ostrza osłabiając nacisk przy dojeżdżaniu do krawędzi forniru.
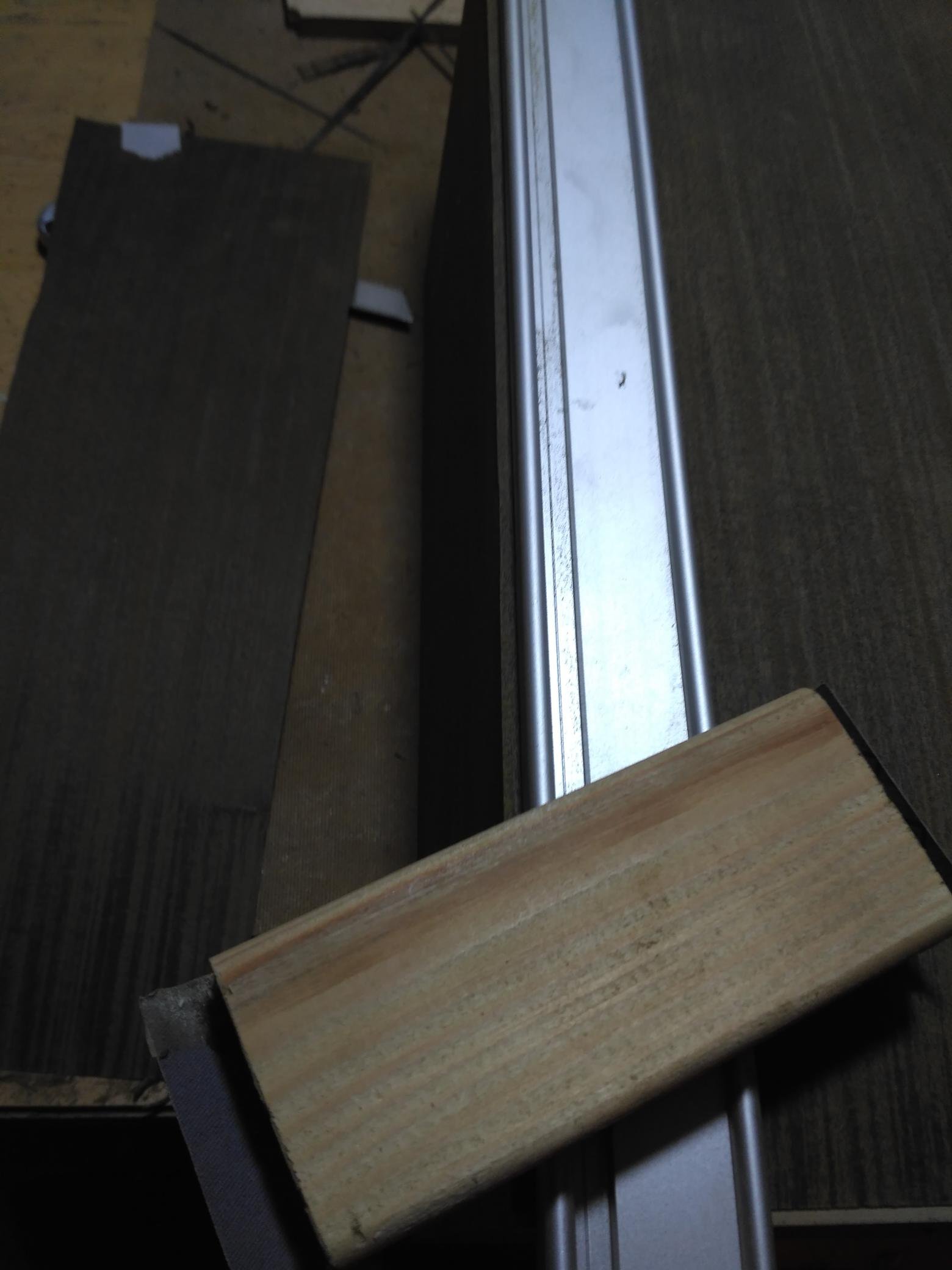
Po nałożeniu kleju. Polecam Evo-Stik Timebond (wysyłąją w Anglobud.pl), poszło z 0,5l, więc warto kupić litr za ok 60 zł.
Sporo mniej śmierdzi, ma konsystencję galaretki/dżemu, a sam fornir po kontakcie dało się jeszcze przez parę sekund oderwać w razie złego przyłożenia - dotyczy to forniru Ipe Lapacho. To dość twardy egzotyk,
który raczej się nie kruszy i dobrze załamywał się na podcięciach. Charakterystyczny wzór sprawia, że wygląda trochę jak modyfik. Fronty fornirowałem jako ostatnie, za poradą Pawła nadmiar forniru obcinałem ostrymi nożyczkami. Pozostałe kilka mm szlifowałem "od czoła"
papierem naklejonym na klocek.
Przy okazji widać plombę niedzielnego fakapu z frezem...
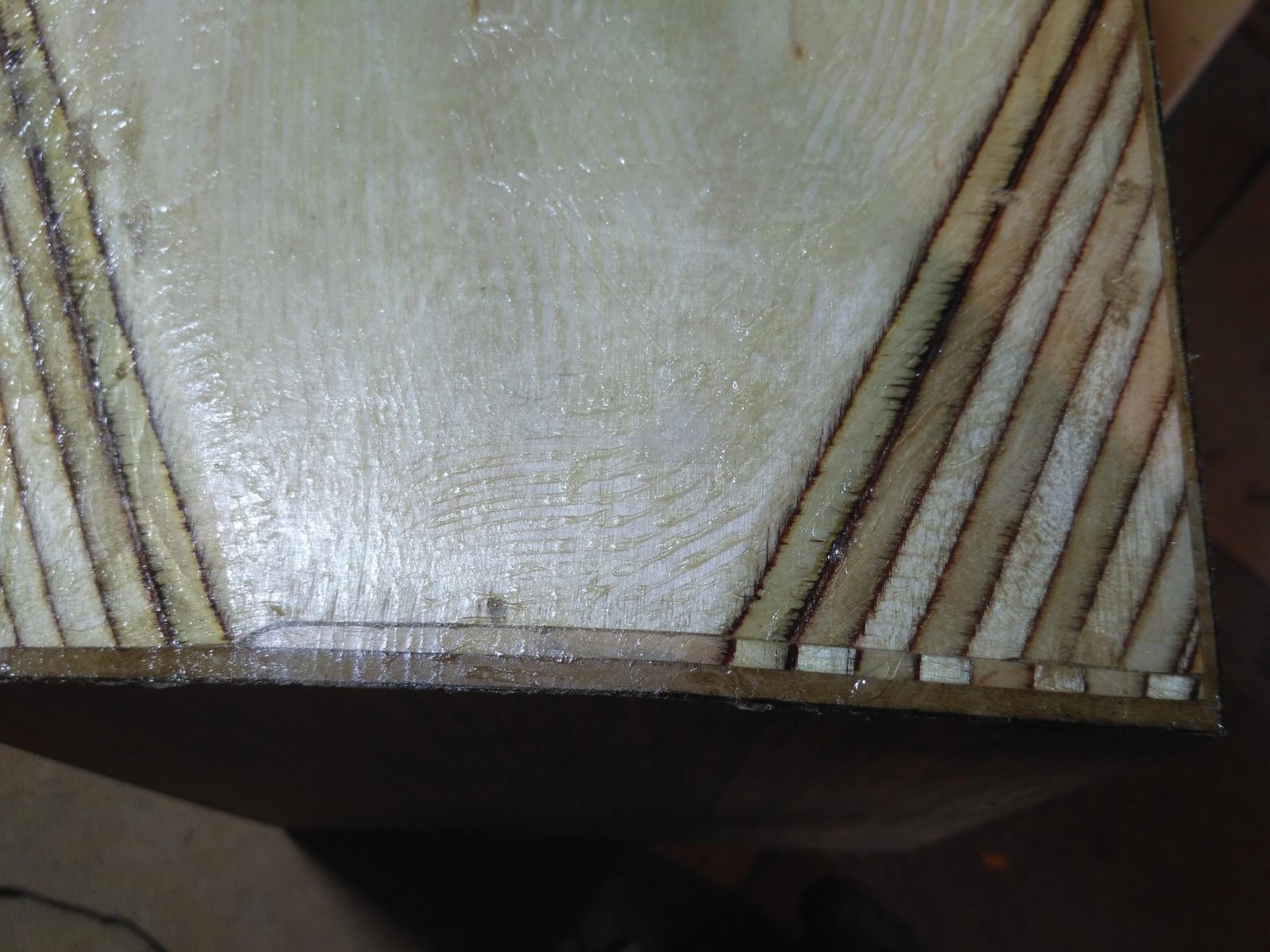
Najpierw podfrezowanie, później wycięcie - bez cyrkla do frezarki ani rusz :)
Warto nie szaleć ze średnicą okręgu i robić przymiarki- ja sądziłem, że zostawiłem margines, a tak na prawdę 1 mm mniej byłoby idealnie.
Pozostało mi pomalować podfrezowanie na czarno.
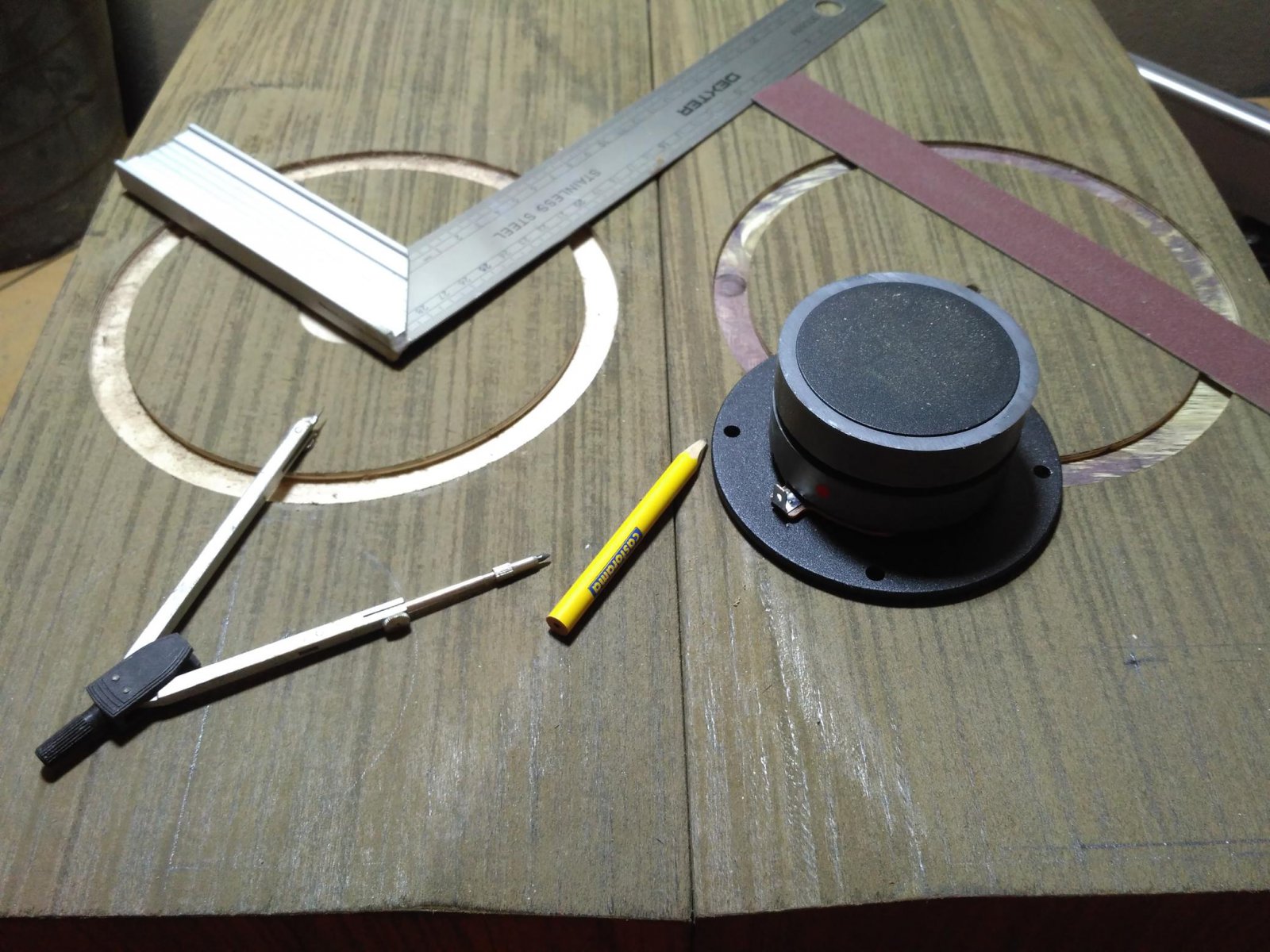
Sprawdzenie regulacji głębokości podfrezowania pod głośnik wysokotonowy.
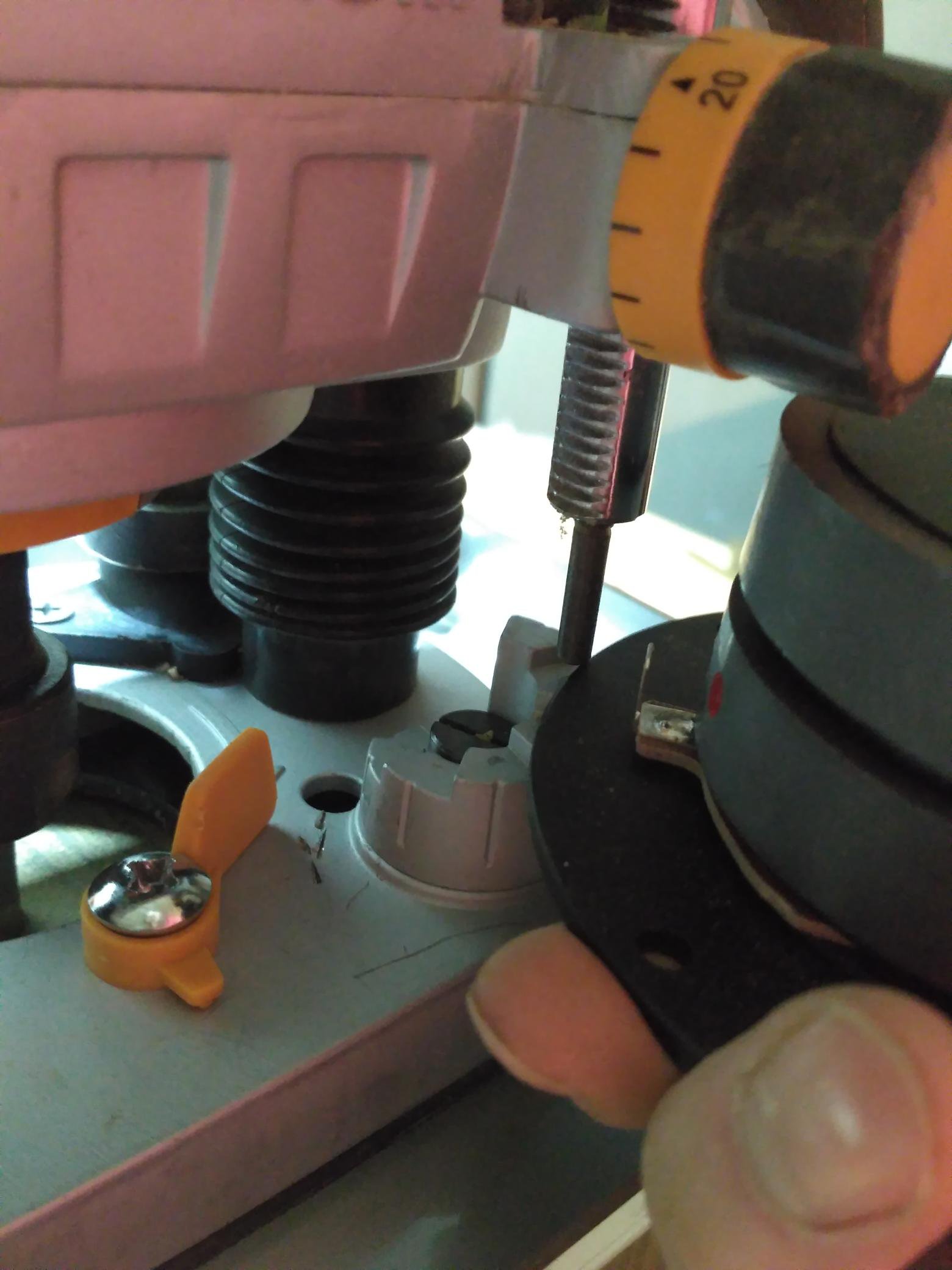
Fotka na szybko, przed wykończeniem powierzchni i wysłaniem 1 szt. na pomiary.
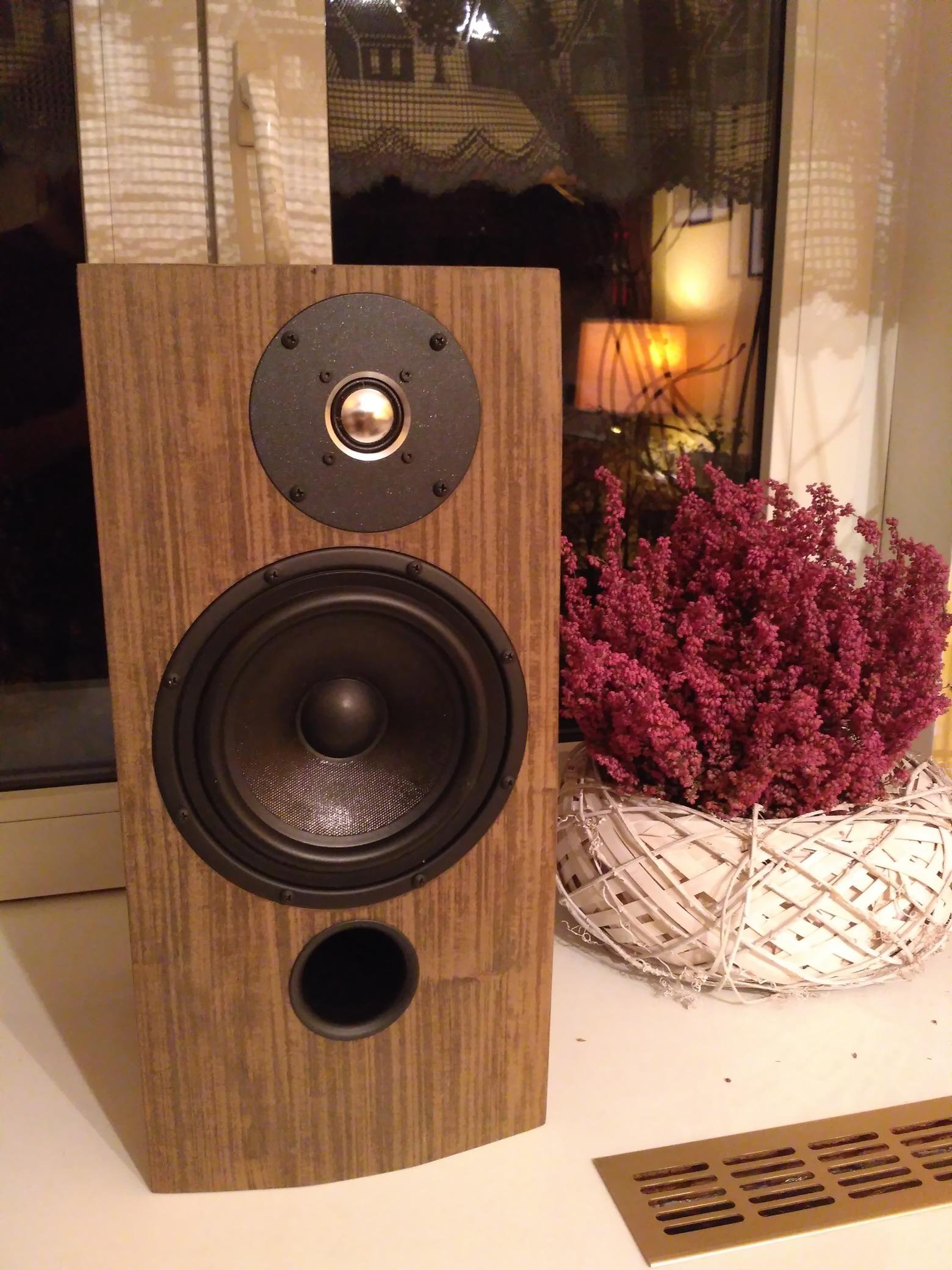
Na razie tyle, jak monitor wróci z pomiarów postaram się w wolnej chwili je wykończyć i pstryknąć lepsze fotki.
Projekt powstał dzięki pomocy forumowicza Branża z zap-audio.pl , który mimo nawału pracy zgodził się zrobić profesjonalne pomiary i zaprojektować filtrację oraz udzielił niezbędnych wskazówek dotyczących samej obudowy.
Dziękuje również Pawłowi S. i Pogromcy Mitów za cenne rady dotyczące budowy i wykończenia.
Wszelkie dane dotyczące budowy zwrotnicy w różnych wariantach oraz rozmieszczenie wytłumienia dostępne tutaj:
http://diyaudio.pl/showthread.php/28...by-Bran%C5%BCa
Materiał - sklejka 15 mm + HDF 3 mm (poza frontem i tyłem)
Wymiary zewnętrzne (po wykończeniu fornirem):
wysokość - 45cm
szerokość - 21cm
głębokość - 26cm
litraż komory 16 litrów netto
ostatecznie zastosowałem jedno poziome wzmocnienie powyżej portu BR
*jak będę miał dostęp do drugiego komputera dodam zwymiarowany rzut aby wszystko było jasne.
Projekt frontu:
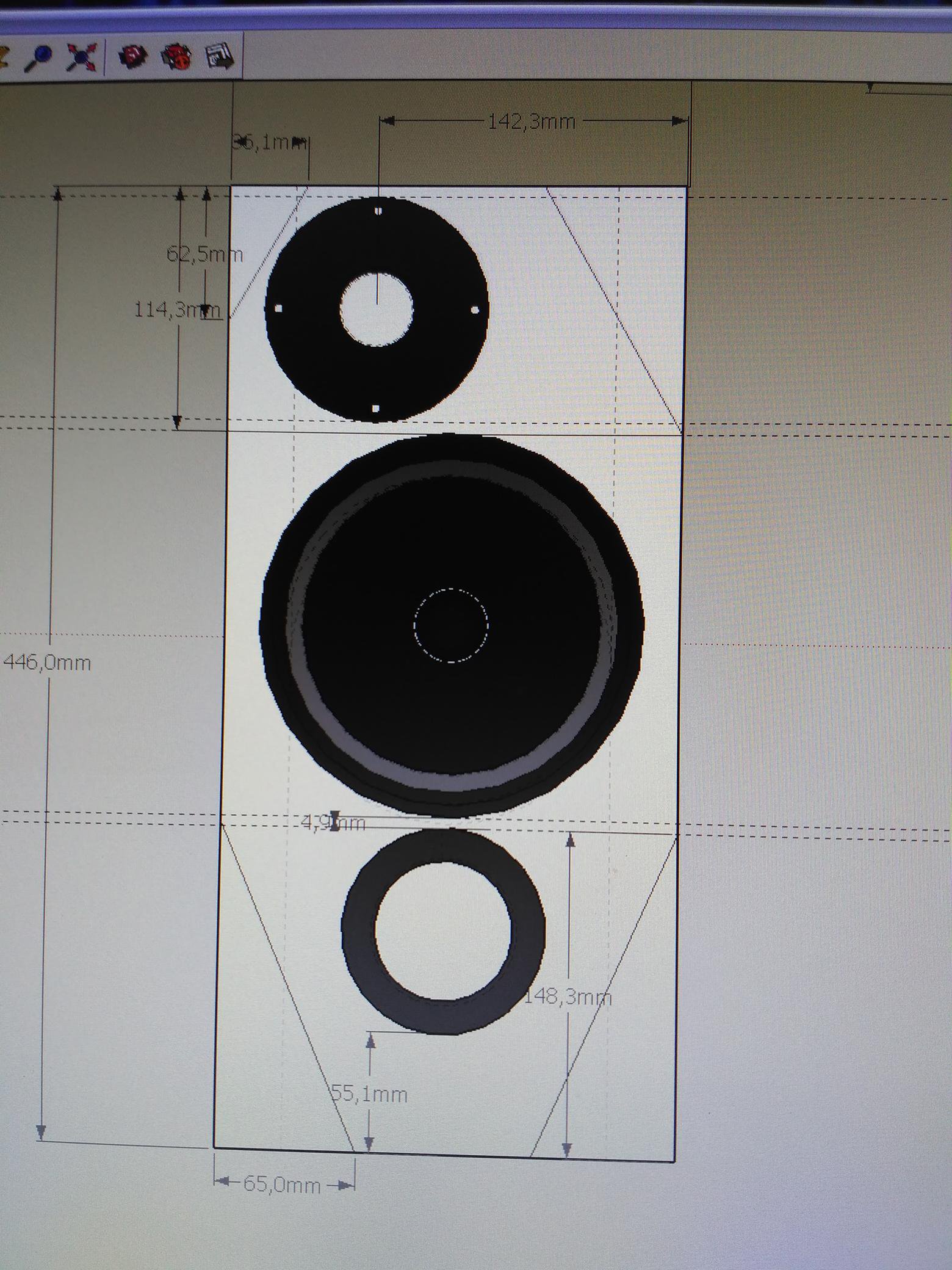
Ponieważ projekt może być ciekawą i niedrogą alternatywą dla początkujących, poniżej opisuje etap budowy właśnie z perspektywy początkującego, uwzględniając
parę pułapek, które każdy doświadczony dobrze zna.
Opis budowy:
Planowałem obudowę z MDF ale w pozostałościach trafił się kawałek sklejki 15 mm.
Zaplanowałem optymalny rozkrój i rozrysowałem go na płycie tak jak w programie czyli liniami pomiędzy którymi prowadziłem ostrze.
Odstępy ok 5 mm ze względu na cięcie zgrubne wyrzynarką średniej jakości, która potrafi ciąć pod lekkim kątem. Opłaciło się, bo margines faktycznie się przydał.
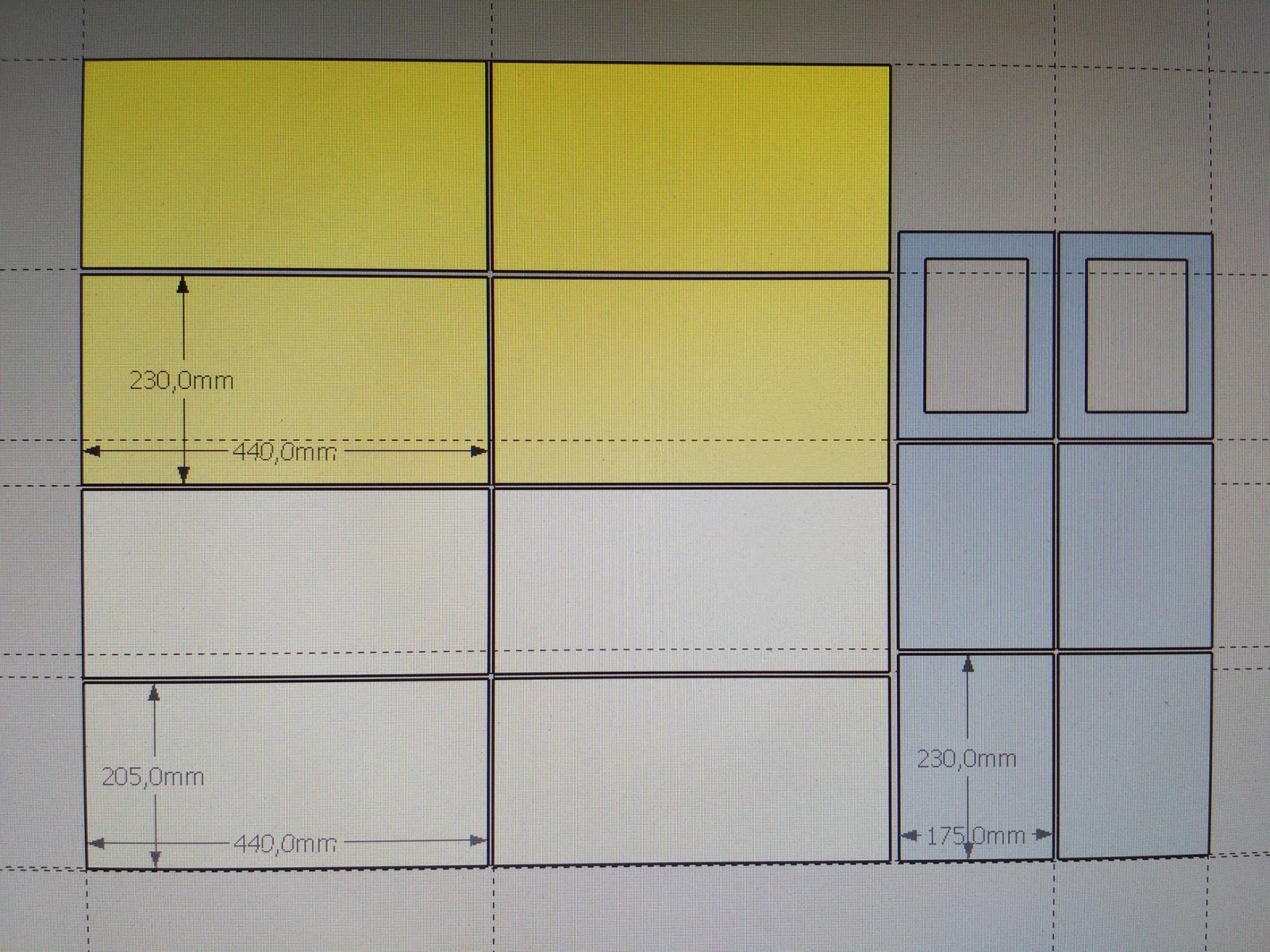
Z aluminiowego kątownika przygotowałem krawędź do frezowania pierwszych elementów.
Jak widać po rozkroju potrzebowałem przygotować jako matryce tylko 3 różne prostokąty - reszta to powielanie.
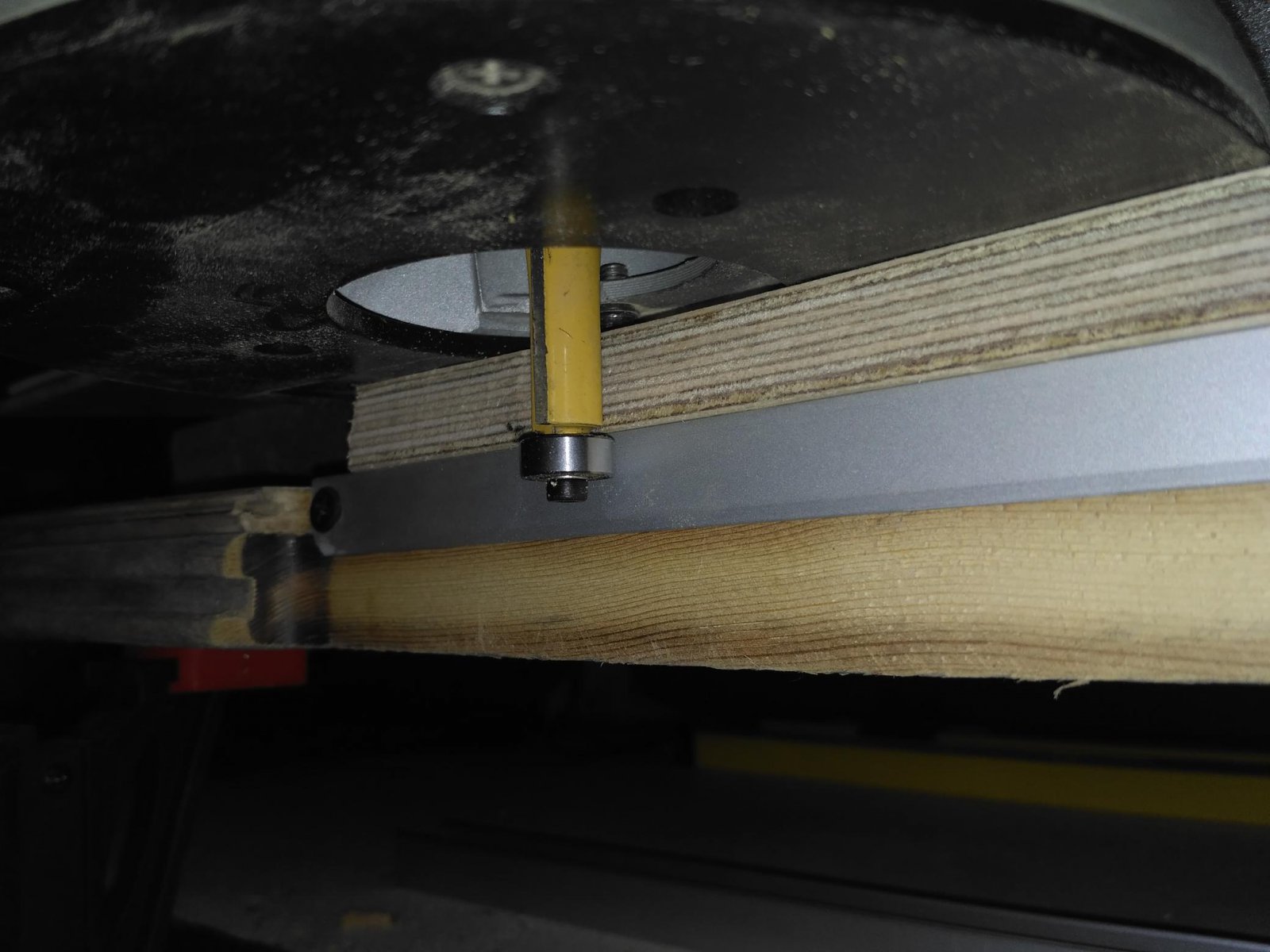
W czasie budowy pomógł mi filmik instruktażowy Pawła:
Kopiowanie kolejnych elementów frezem kopiującym- jednoręczny ścisk bardzo ułatwia pracę w pojedynkę (użyłem najtańszych z Casto za 15 zł/szt ).
Nie polecam zestawów żółtych frezów z allegro - są liche i większości pewnie nigdy nie użyjecie. Hard Head z Juli dają radę i są na sztuki.
Aby lepiej ustabilizować większe elementy przekładałem je papierem ściernym.
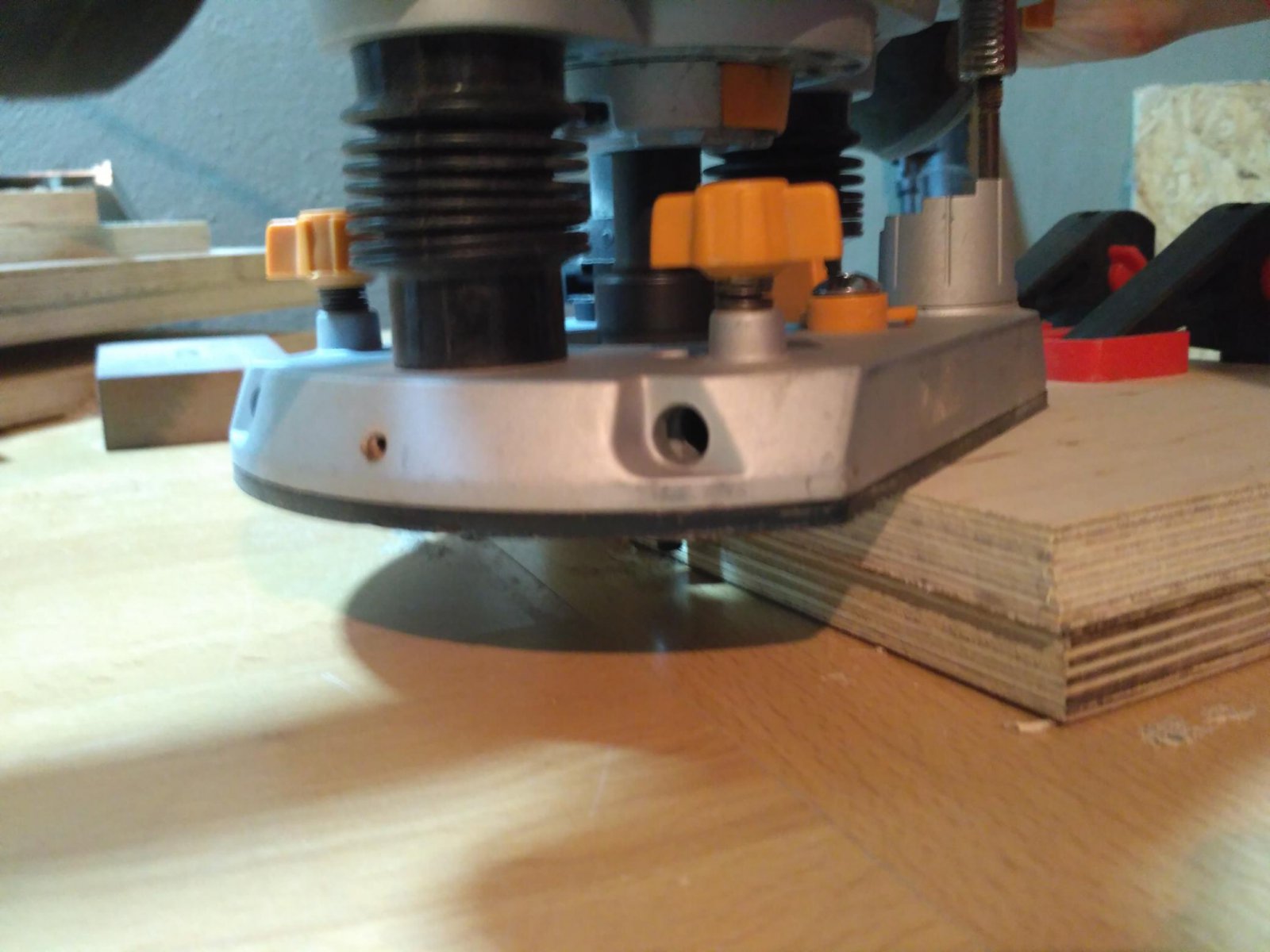
Ponieważ kupiłem gniazda z krótkim gwintem musiałem wyfrezować rowek po wewnętrznej stronie tylnych ścianek.
Wymierzyłem odległości rowka od krawędzi i zapisałem aby po ofornirowaniu wiedzieć gdzie wiercić.
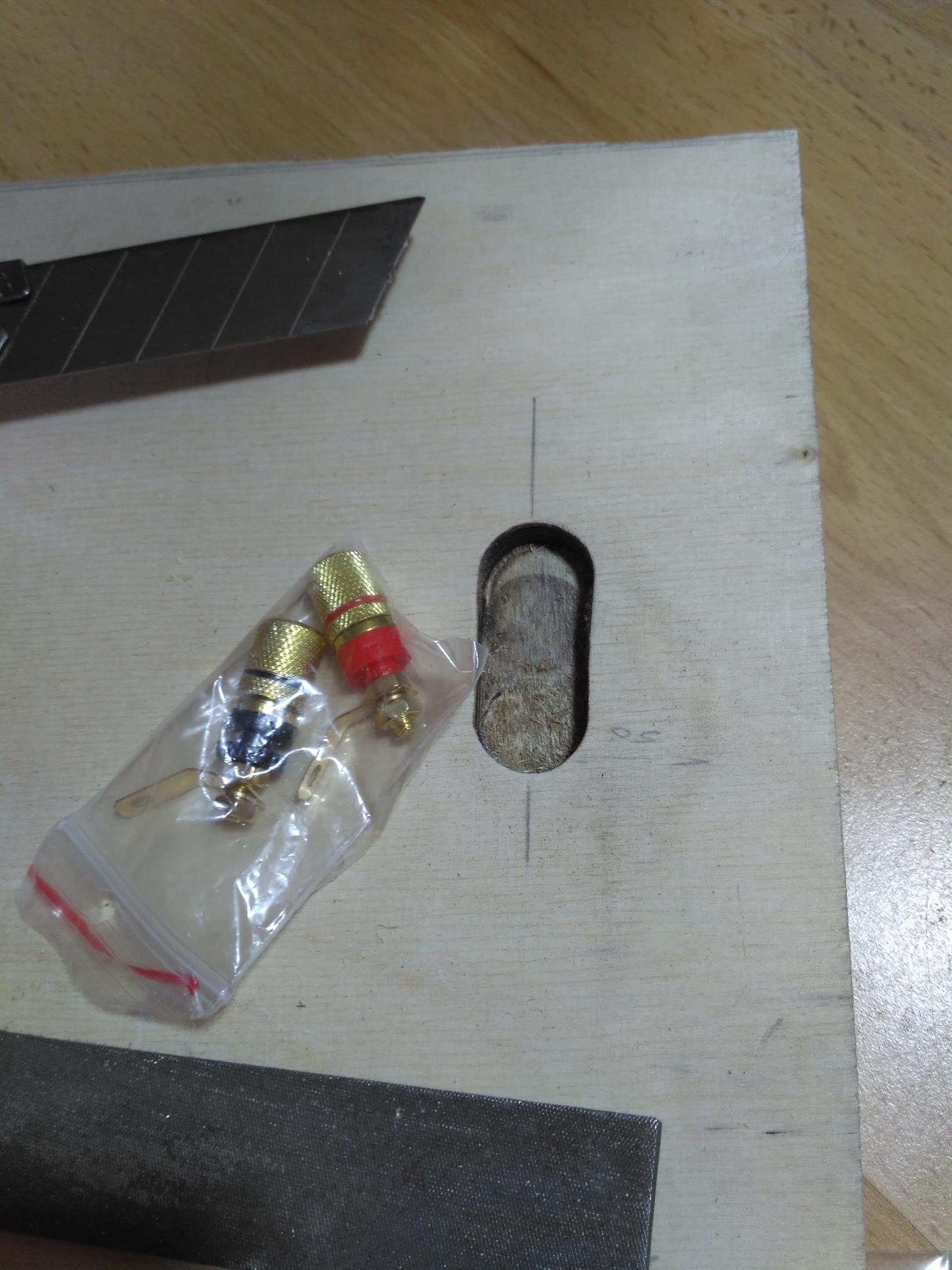
Rozpocząłem składanie. Kątowe ściski Wolfcraft bardzo się przydały. Używałem wkrętów do drewna,
które po związaniu wykręcałem. Otworki po wkrętach na tyłach i frontach (nie były oklejane HDFem) zaszpachlowałem
wiórami z klejem.
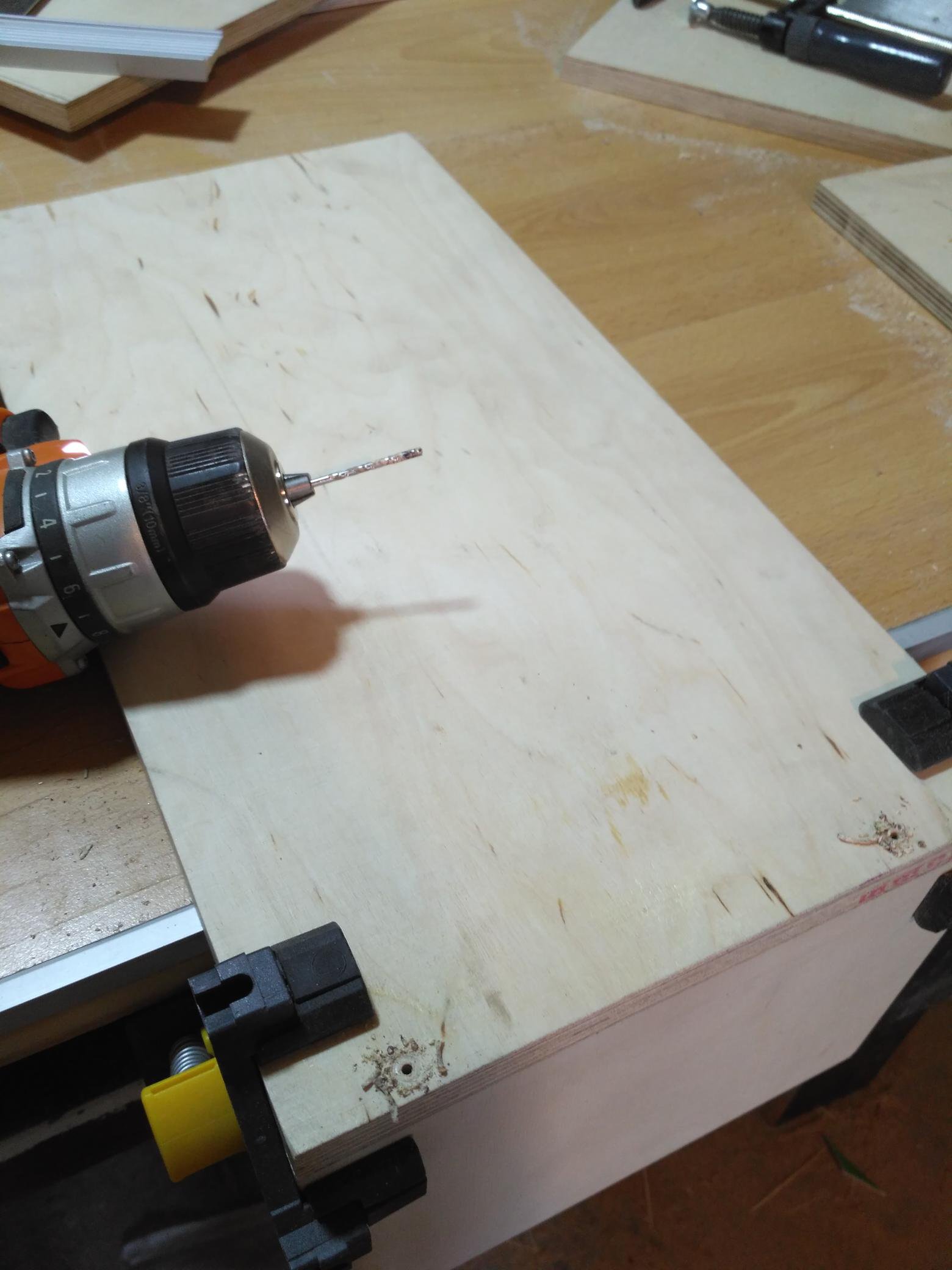
Przygotowanie wzmocnień. Ponieważ miały być możliwie w połowie wysokości kolumny, widać podcięcie na dolną część kosza głośnika średnio niskotonowego.
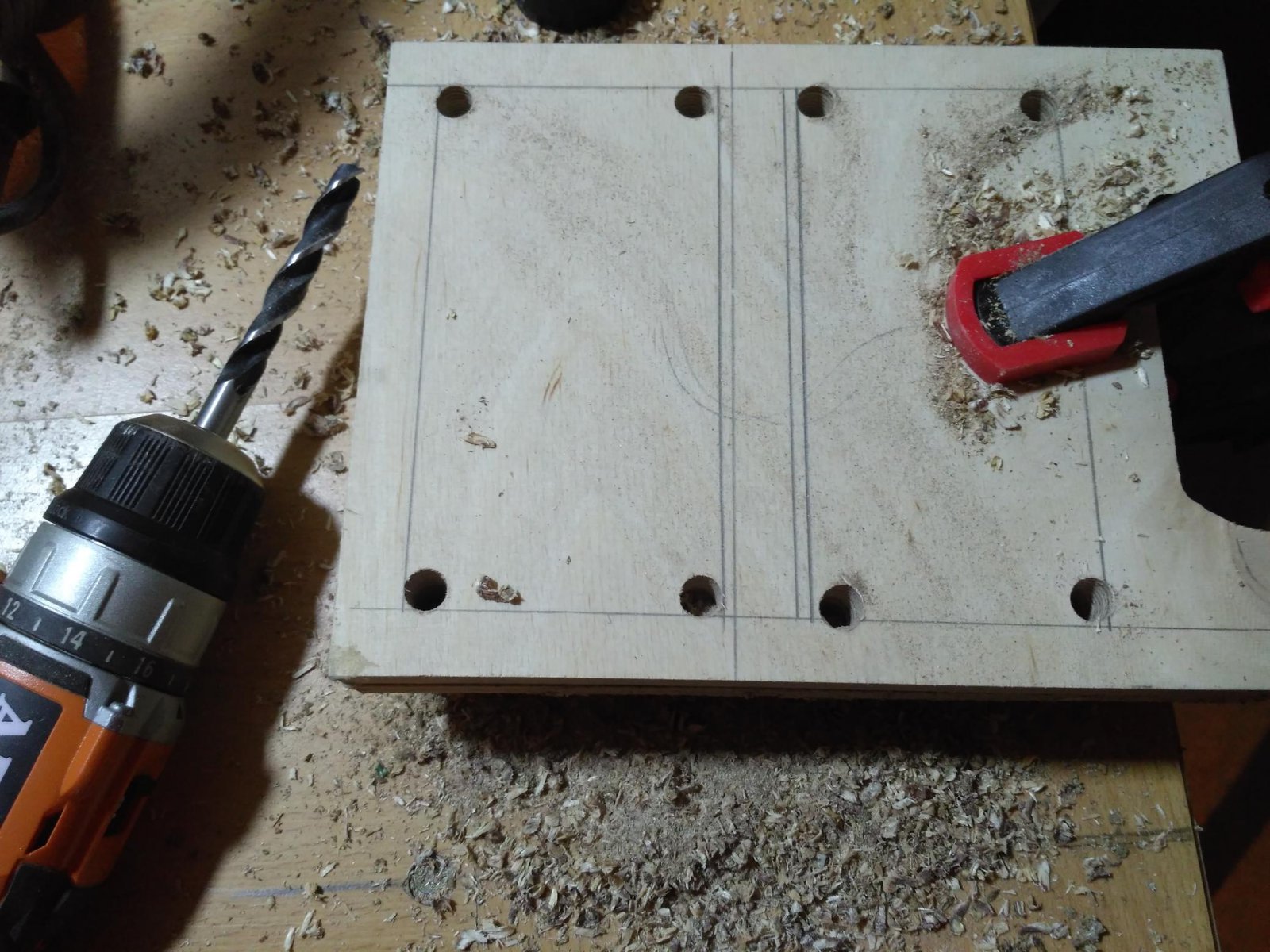
Wklejanie wzmocnień - przy okazji widać trójkąty wklejone w miejscach planowanych ścięć frontów (poza małym ścięciem przy wysokotonówce). Nie zrobiłem podwójnej ścianki frontowej
ponieważ nie chciałem zwiększać wymiarów kolumn.
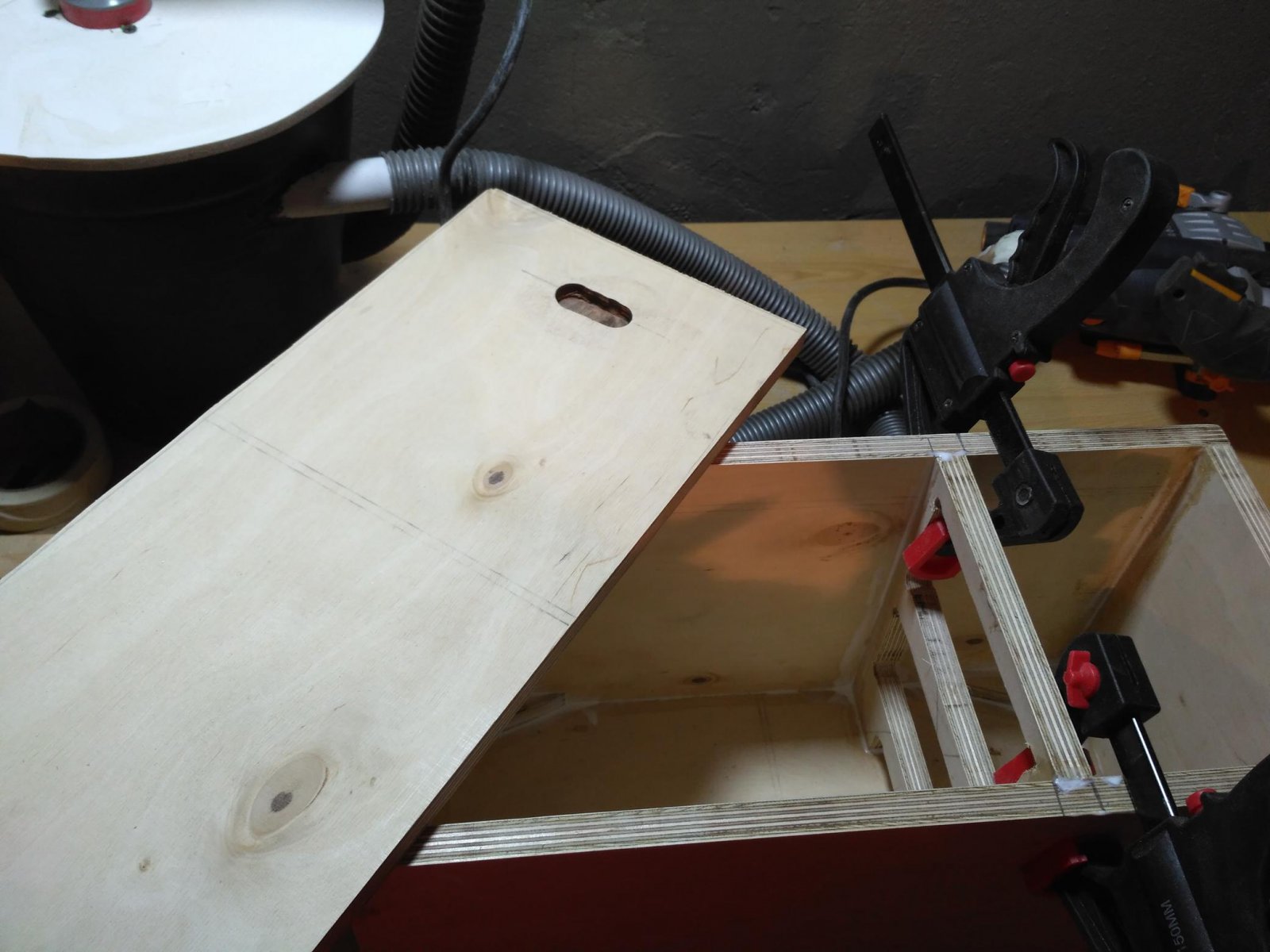
Tak się kończy frezowanie w niedzielę - na szybko, żeby jedynie umiarkowanie w*rwić neurotyczno-kompulsywną sąsiadkę z Zespołem Tourett'a...
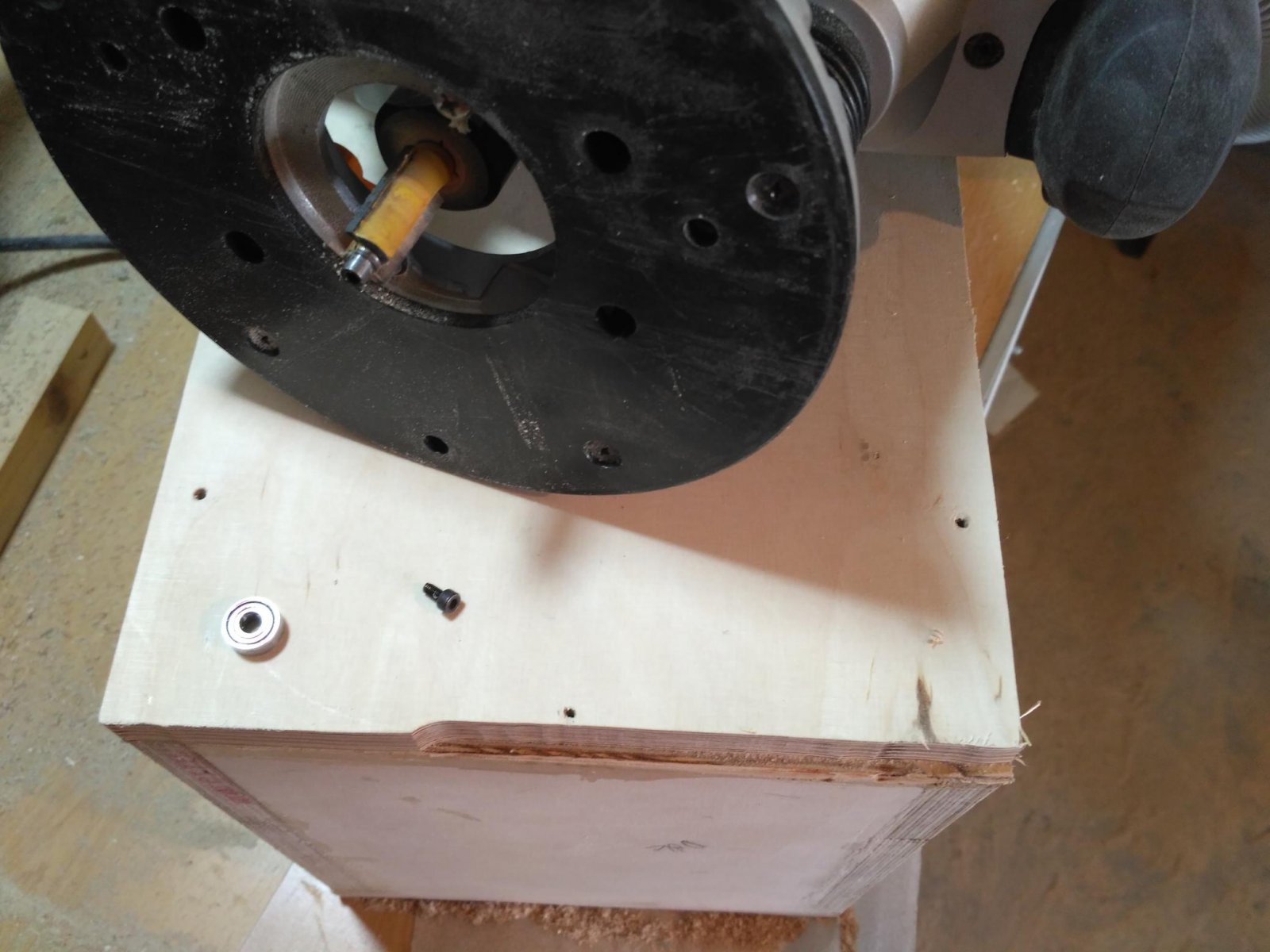
W poszukiwaniu Świętego Graala DIYowców, czyli "fosfatowanych wkrętów z niestożkowym łbem w cenie tych ze stożkowym"...
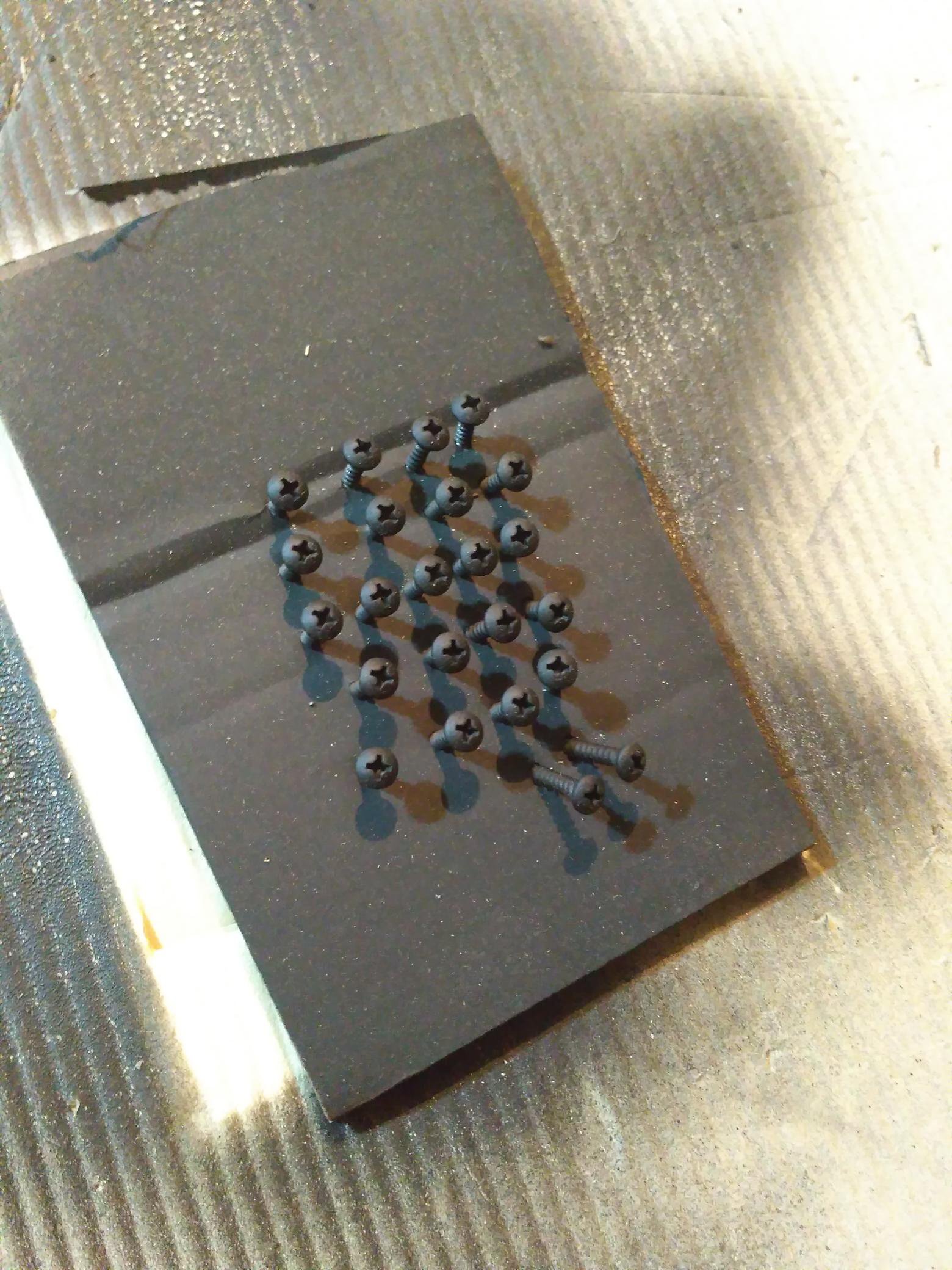
Etap oklejania płytami HDF (przeciwdziałanie klawiszowaniu). Aby płyty nie rozjeżdżały się przy docisku
stabilizowałem je listewkami przybijanymi na zszywki - sprawdziło się dobrze, ale warto pamiętać o zabezpieczeniu krawędzi kolumny przed wyciekającym klejem taśmą malarską.
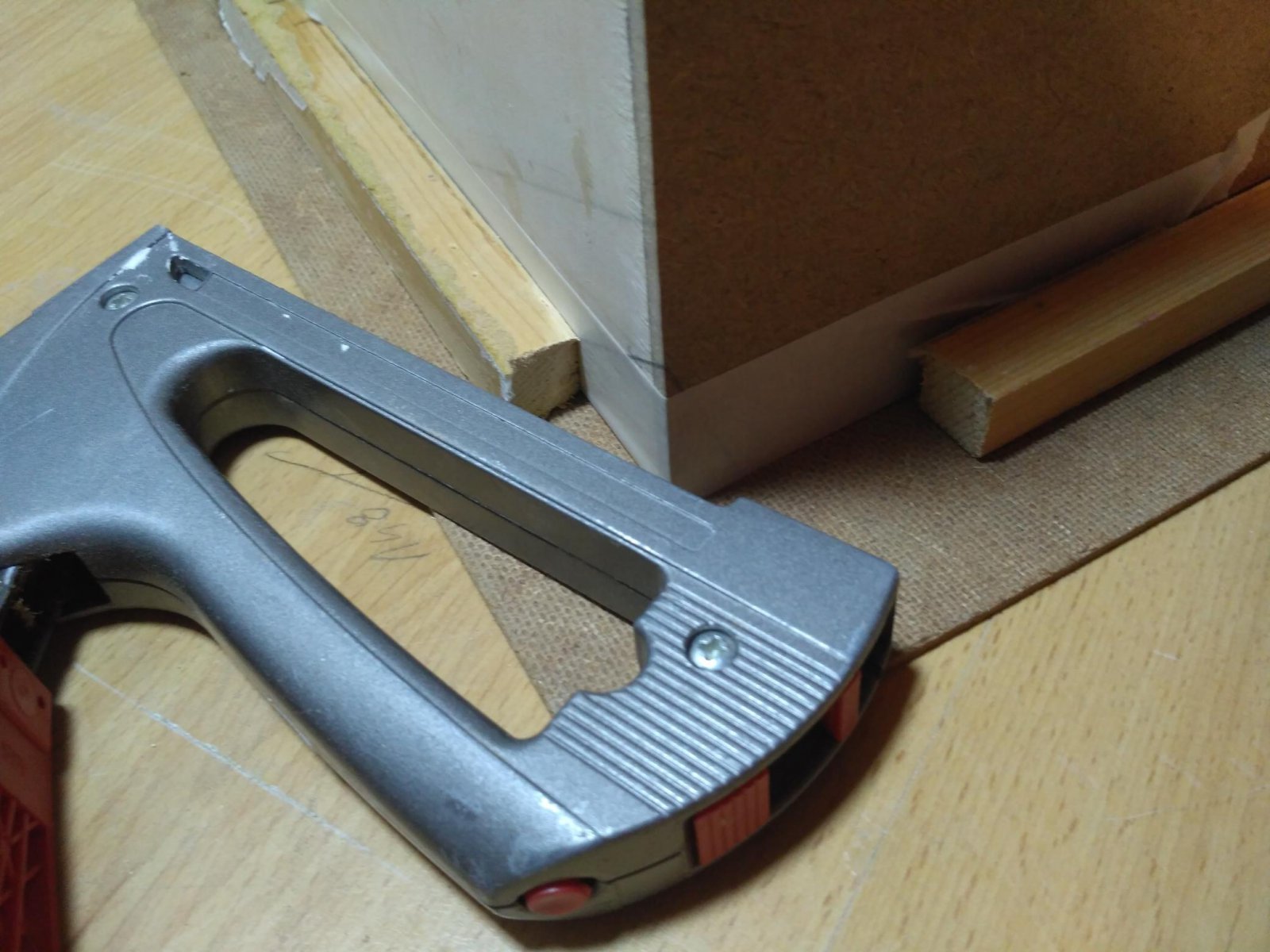
Jako przekładki użyłem piankowych płyt pod panele. Pod kołami też jest obciążenie - prasa godna Gutenberga.
Ze względu na klej zdobiący festonami ścianki z ochotą wprost proporcjonalną do generowanej siły nacisku, warto zawczasu cenzurować szmatką.
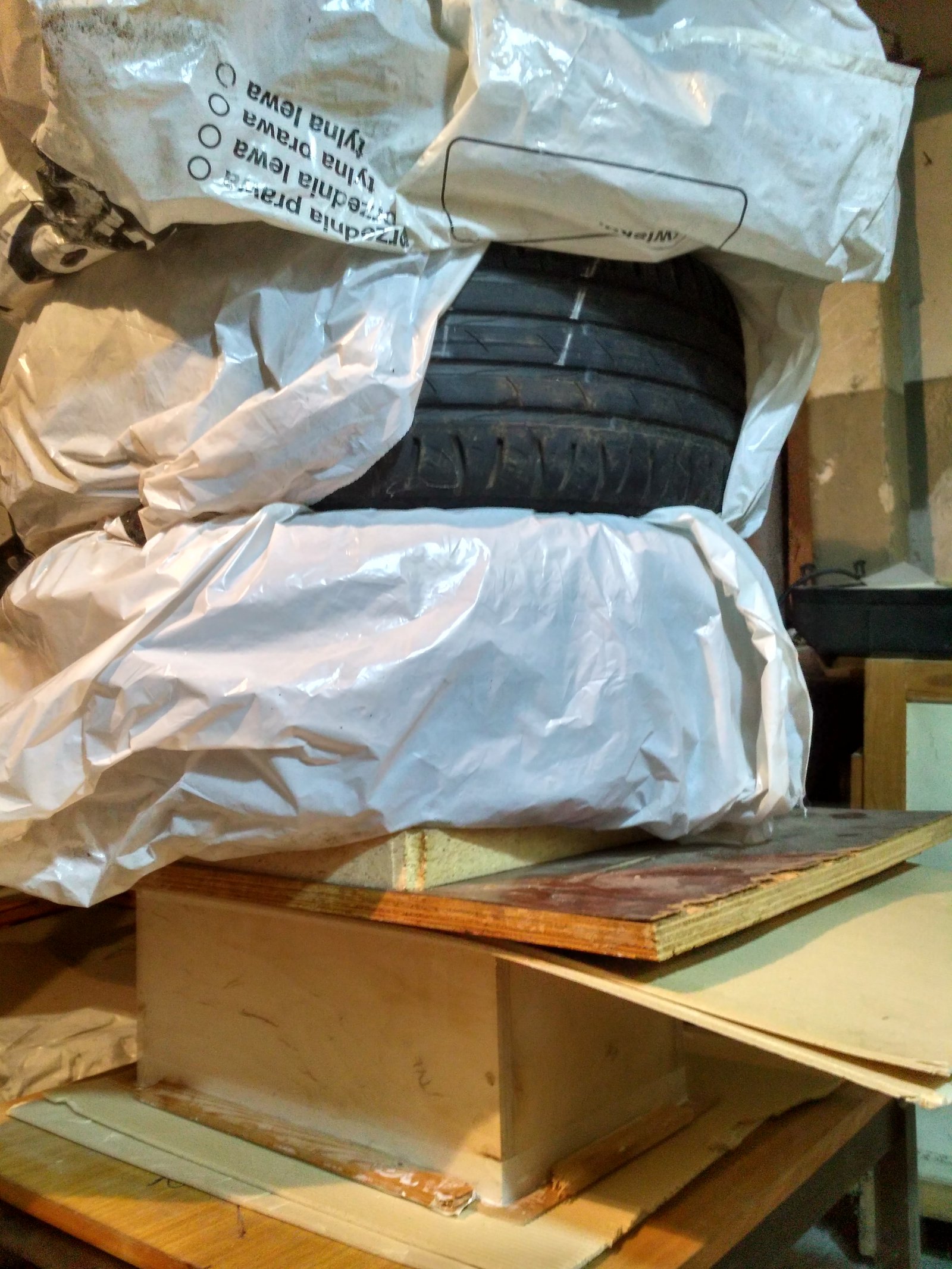
...pół-maska Irudek - polecam ze względu na tanie, nakładane na filtry pady przeciwpyłowe (ok 3zł/para) .
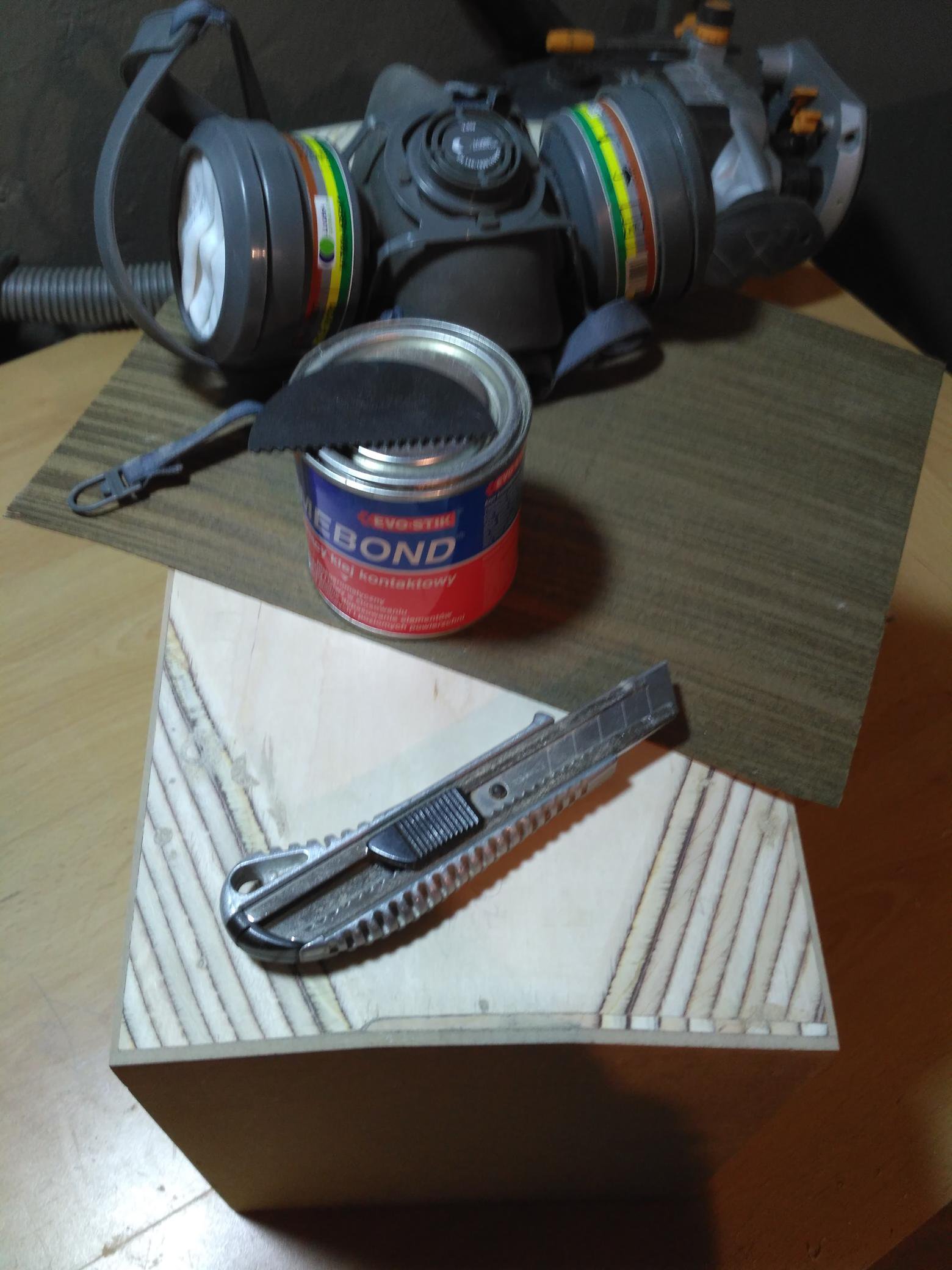
Przygotowanie forniru - warto zrobić sobie przymiar podklejony papierem ściernym, żeby nie jeździł i używać nożyka z okrągłym ostrzem.
Każdy odcinek ciąłem po kilka/kilkanaście przebiegów ostrza osłabiając nacisk przy dojeżdżaniu do krawędzi forniru.
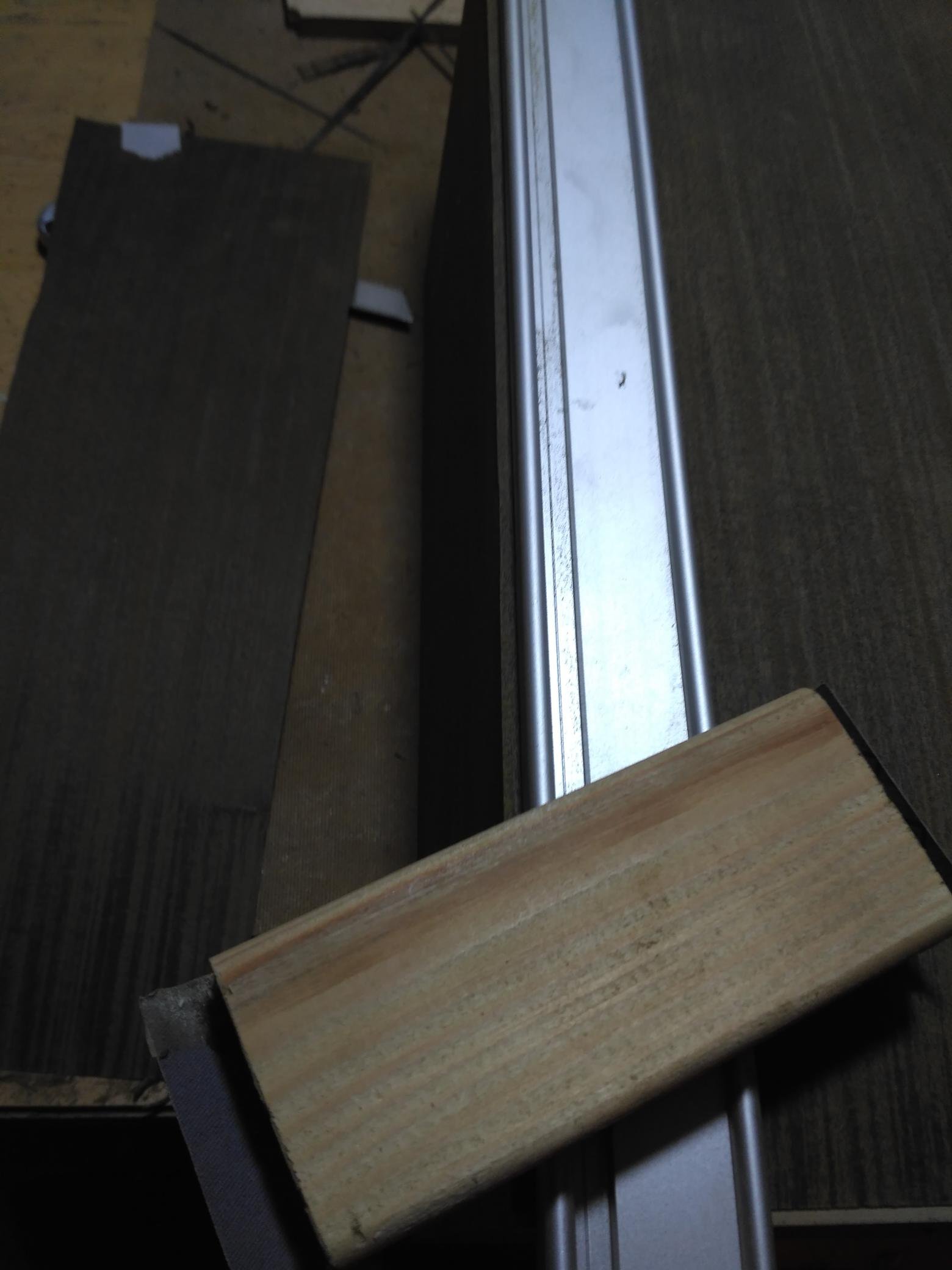
Po nałożeniu kleju. Polecam Evo-Stik Timebond (wysyłąją w Anglobud.pl), poszło z 0,5l, więc warto kupić litr za ok 60 zł.
Sporo mniej śmierdzi, ma konsystencję galaretki/dżemu, a sam fornir po kontakcie dało się jeszcze przez parę sekund oderwać w razie złego przyłożenia - dotyczy to forniru Ipe Lapacho. To dość twardy egzotyk,
który raczej się nie kruszy i dobrze załamywał się na podcięciach. Charakterystyczny wzór sprawia, że wygląda trochę jak modyfik. Fronty fornirowałem jako ostatnie, za poradą Pawła nadmiar forniru obcinałem ostrymi nożyczkami. Pozostałe kilka mm szlifowałem "od czoła"
papierem naklejonym na klocek.
Przy okazji widać plombę niedzielnego fakapu z frezem...
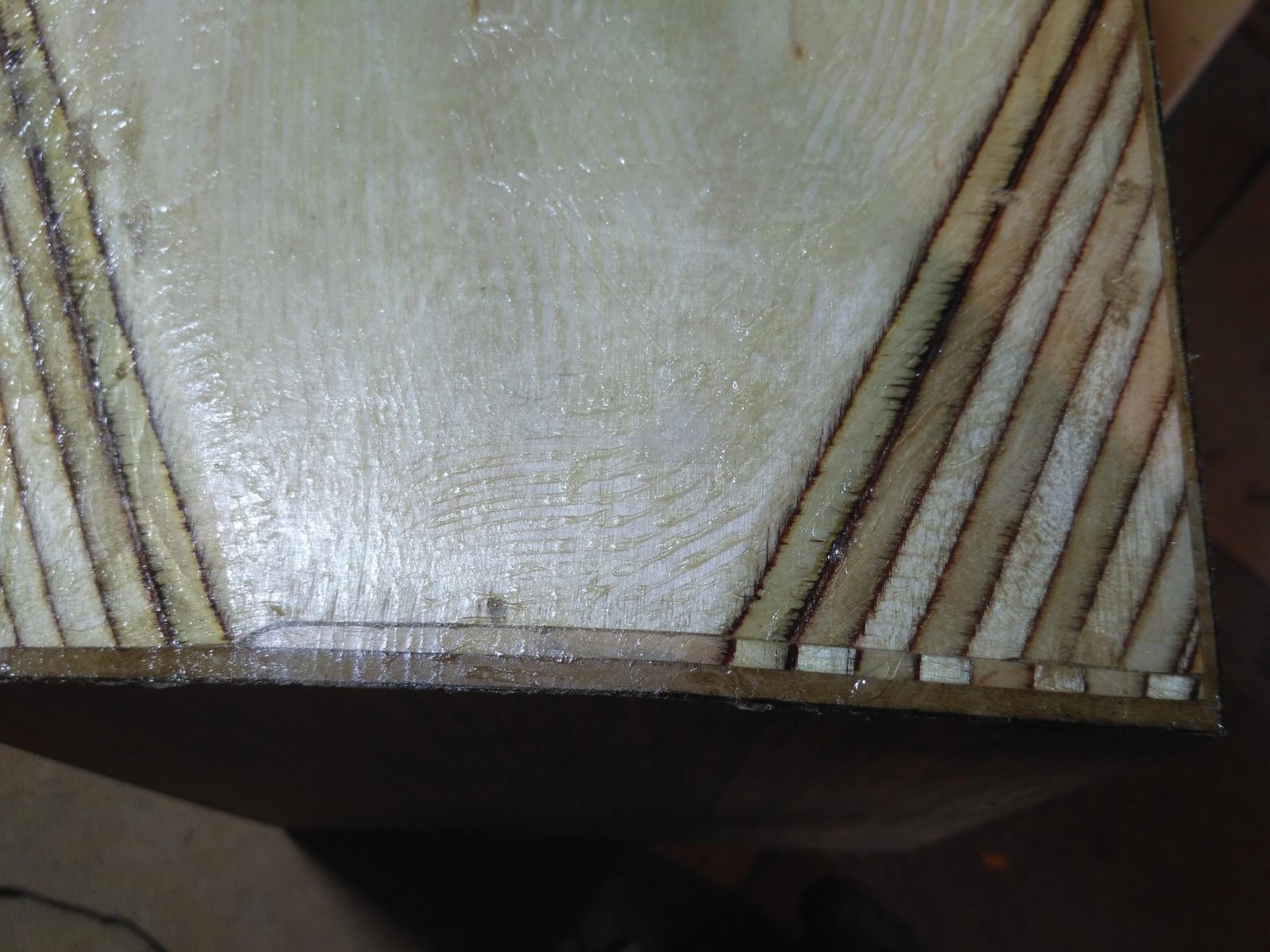
Najpierw podfrezowanie, później wycięcie - bez cyrkla do frezarki ani rusz :)
Warto nie szaleć ze średnicą okręgu i robić przymiarki- ja sądziłem, że zostawiłem margines, a tak na prawdę 1 mm mniej byłoby idealnie.
Pozostało mi pomalować podfrezowanie na czarno.
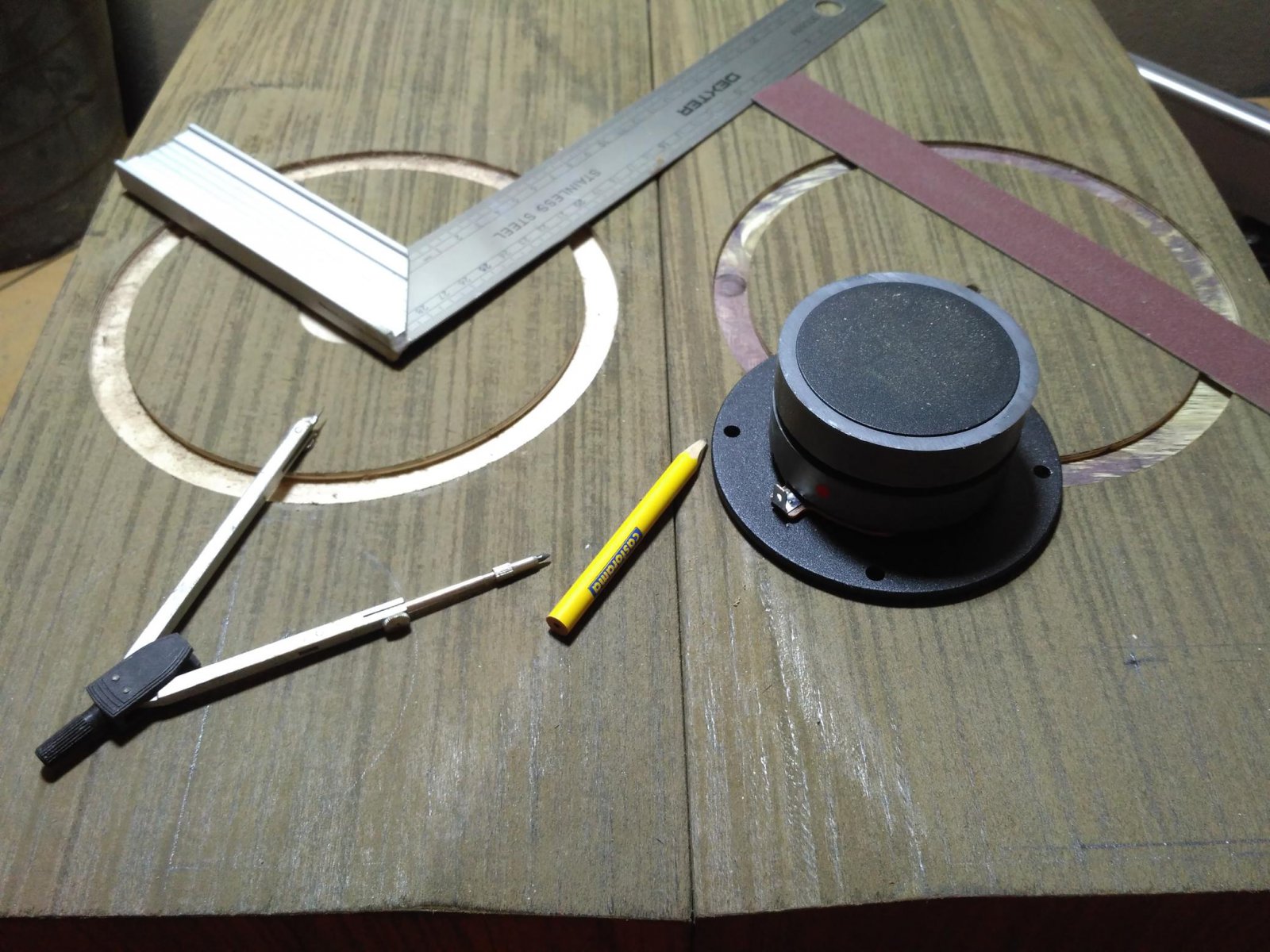
Sprawdzenie regulacji głębokości podfrezowania pod głośnik wysokotonowy.
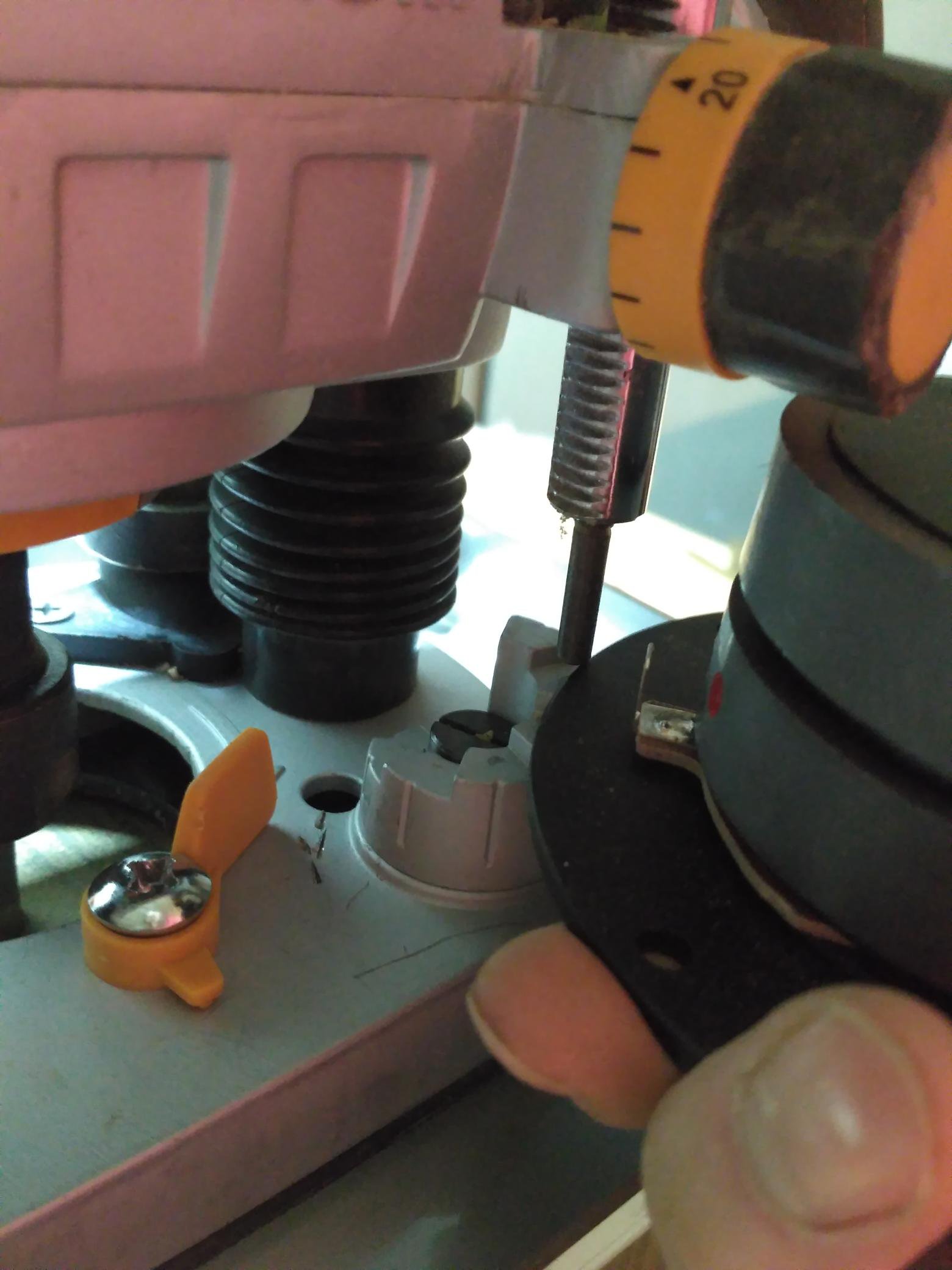
Fotka na szybko, przed wykończeniem powierzchni i wysłaniem 1 szt. na pomiary.
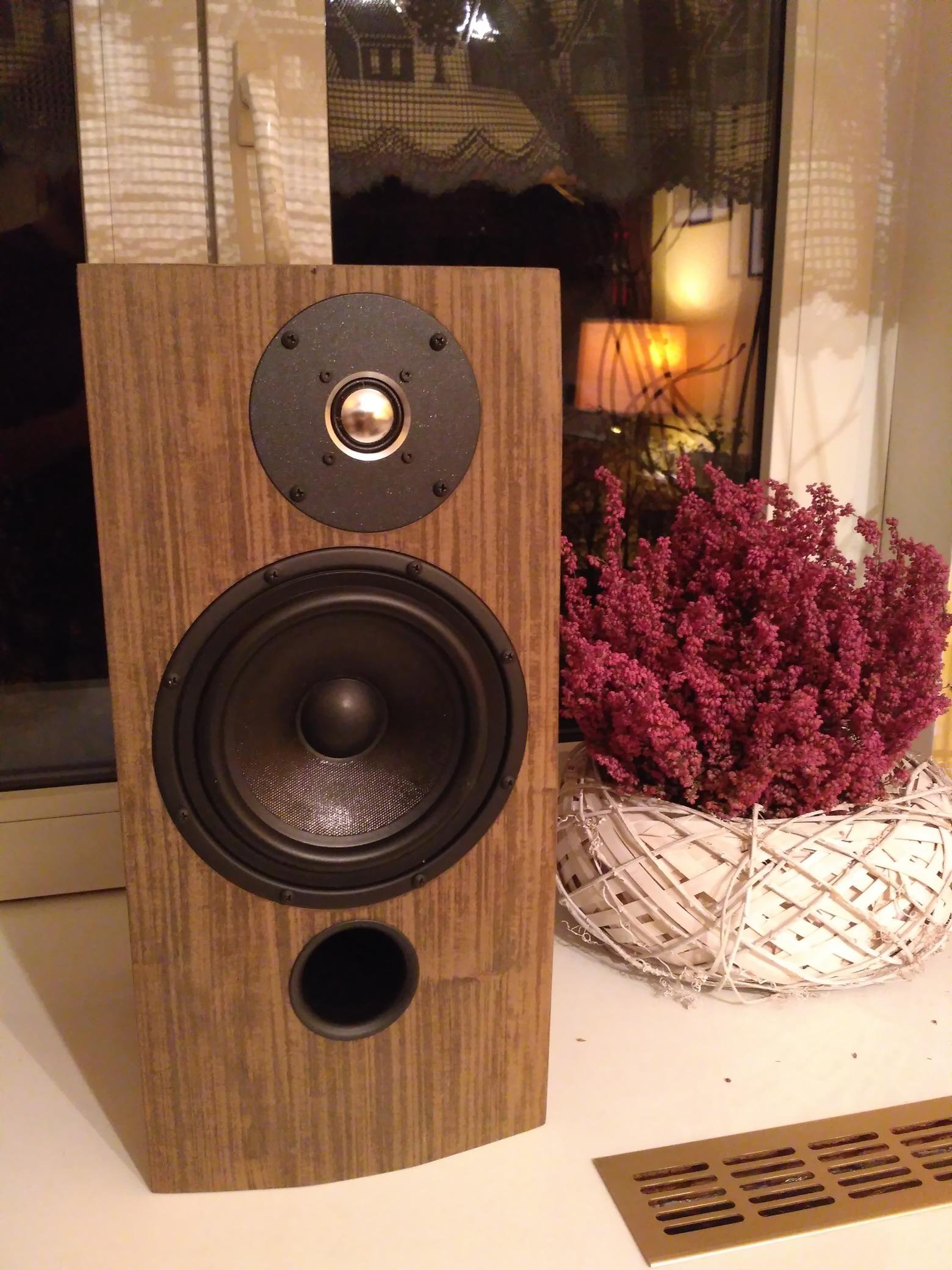
Na razie tyle, jak monitor wróci z pomiarów postaram się w wolnej chwili je wykończyć i pstryknąć lepsze fotki.
Skomentuj